Hello,
Within the last 2 months or so our FSM system has been creating additional part needs for place & locations that are already at their min/max. This is not consistent for all parts or places and I have no idea what else to look at. Any insight of where to start looking would be great! Our replenishment process has not changed at all. I’ve included three screen shots of one part_id in a few screens to also show that in the “On Demand” hyperlink qty it is showing a qty of (1) but when clicking on that link, there are 3 different part needs out there.
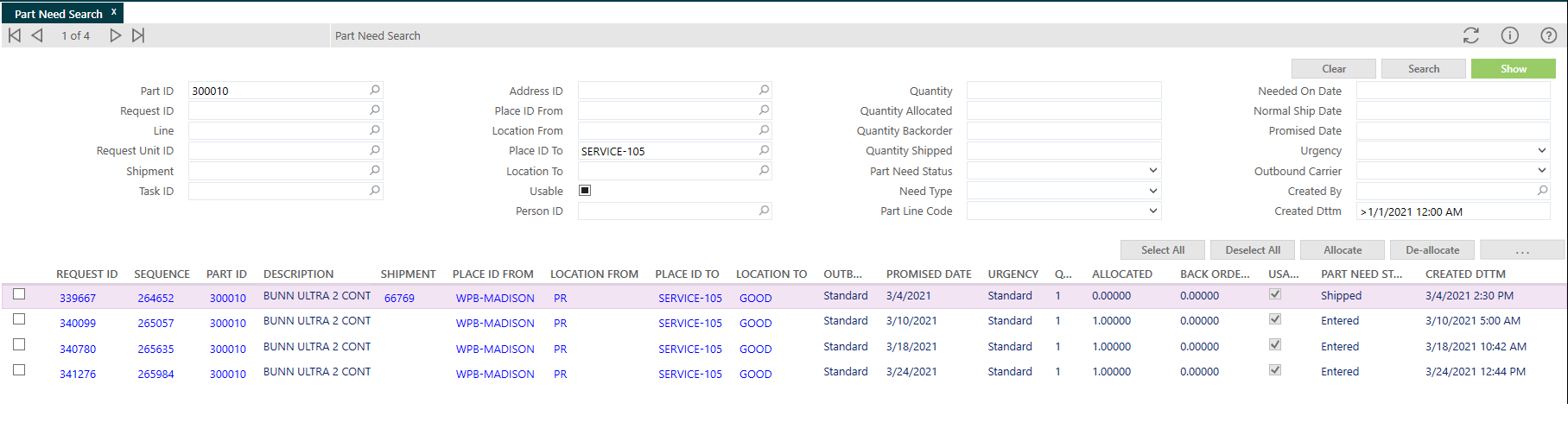
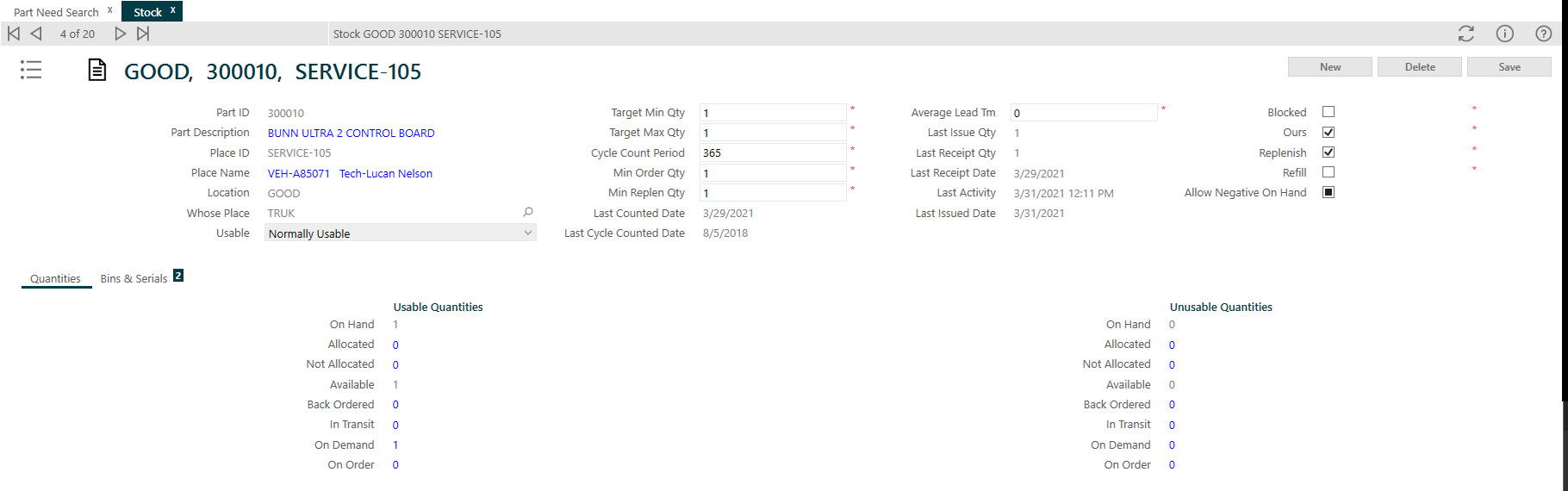
