Does anyone have any info/documentation/knowledge, please, on Transaction Revaluation Events?
We’re in Apps9, running weighted average costing.
This is an OOREC/Receipt of Shop Order transaction for a Shop Order connected to a Project. It’s the first time we have manufactured the part. I don’t think that’s partiularly relevant as there are other OORECs with Reval Events on parts we have manufactured multiple times.
The total cost of the shop order is the 3506.86 (3336.46+170.4) and the part’s current inventory value is 3506.86. The part was subsequently issued at 3506.86.
Material Cost on the SO was 2086.59, Op Cost was 1420.27. Why did it not just OOREC at 3506.86? Where does this 3336.46 come from?
I’m sure the answer will be blindingly obvious …
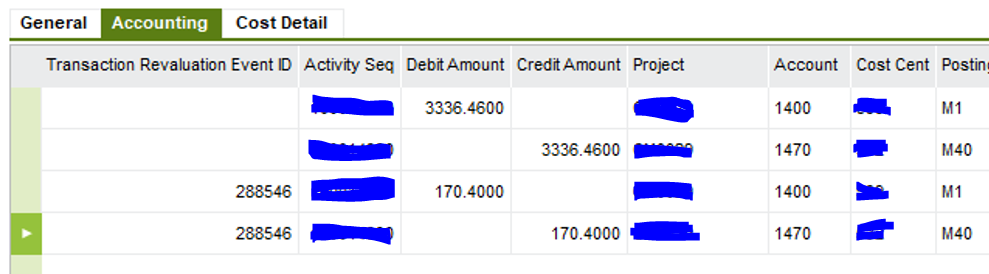
Thanks in advance!