For reasons we do not understand, we have a shipment that appears in IFS as not shipped. But it has physically been shipped (not in IFS), invoiced (in IFS) and paid (in IFS).
Now we have 422 parts left in the “Inventory Parts in Shipment Inventory”, all linked to shipment 94! Shipment 94 is a consolidation 21 different customer orders all meant for the same customer in one huge shipment.
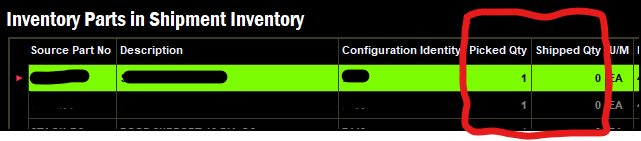
First thought was to simply scrap the parts for each line of the “Inventory Parts in Shipment Inventory” that should no longer be there but we get the following error message:
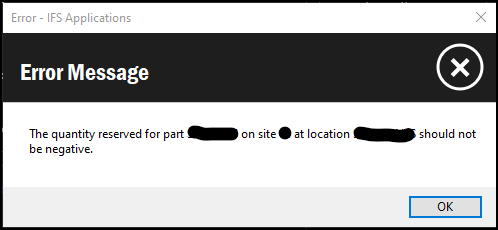
If we try to return the part in inventory (we could then do a cycle count to 0): we get this error message:
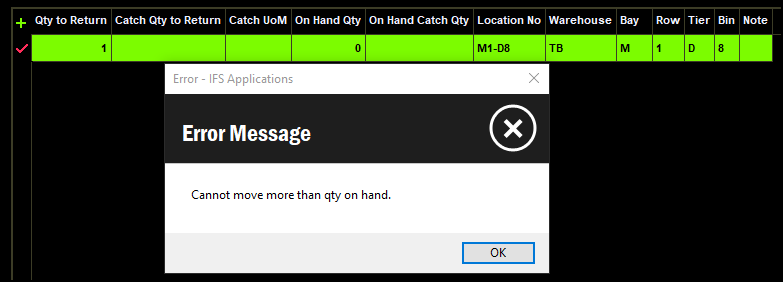
We Make-to-Order but we should at least have the one part that is supposedly still at our shipment location!
What can we do to get those parts out of “Inventory Parts in Shipment Inventory”?