Hello All,
I am looking at connecting a part to a production line so I can use the unscheduled receipts function to convert unsterile manufactured parts into sterile parts with minimal admin. The steriliser is run several times a day, with multiple parts, so using Shop Orders would create a lot of admin work.
The Sterile parts have a forecast and are Master Scheduled. The production receipts for the sterile parts are created manually, as are the Shop Orders for the unsterile parts, but I want MRP to generate the Purchase Requisitions for the components based off the forecast.
I’ve set up a stucture like below, and tested out and all seems to be working as I hoped. However, the help function for the Production Line is confusing me - it suggests MRP is cancelled when it reaches a Production Line part, but this is not what I am seeing.
From Help Page:
“Demand for parts manufactured in the production line is broken down into demand for their components. MRP is canceled when it reaches the production line part.”
Although everything is working as I would like, I want to make sure I understand what is happening and why. Have I missunderstood what the Production Line help is describing? Is it because I am using Master Scheduling?
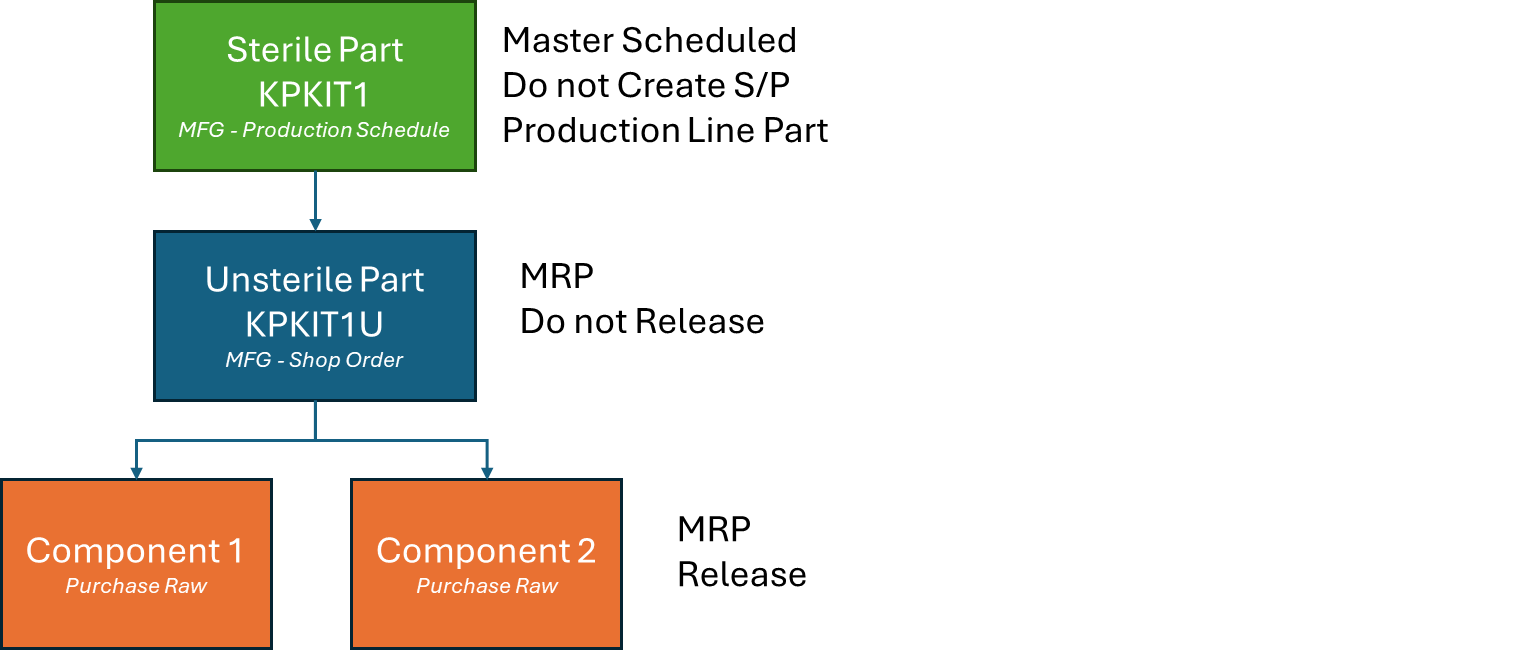
I have only created a forecast, no actual Shop Orders/Production Schedules
MRP Top Down Page - Gross Requirements for Sterile Part:
Demand from MS Forecast / MS Supply (s/p set to do not create)
PTF =16th Jan
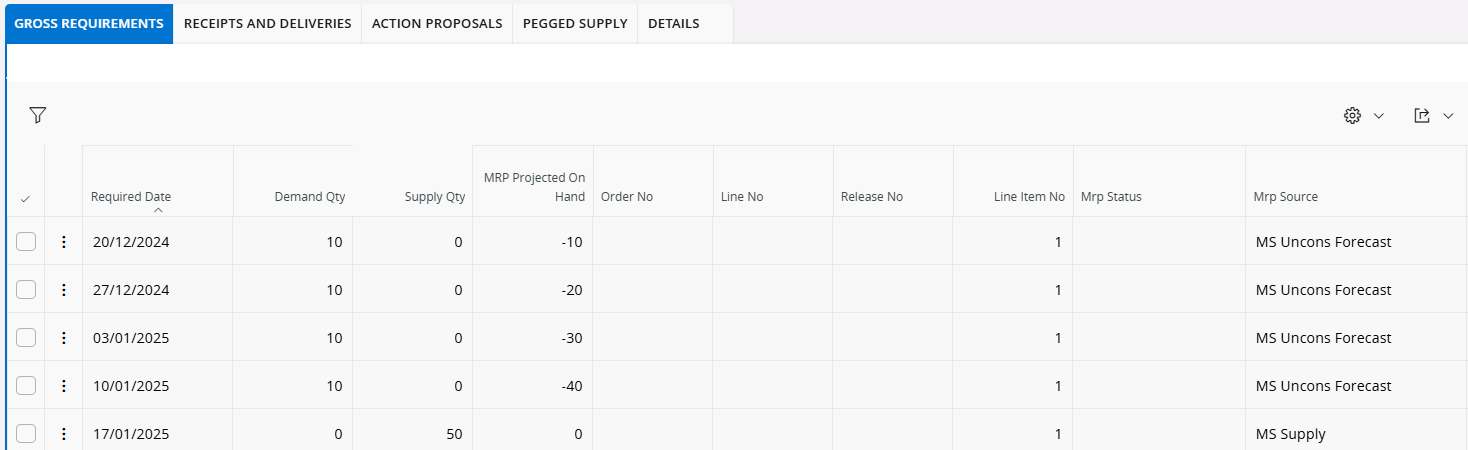
MRP Top Down Page - Gross Requirements for Unsterile Part:
Demand from MS Proposal / Supply Exploded but no requisition generated
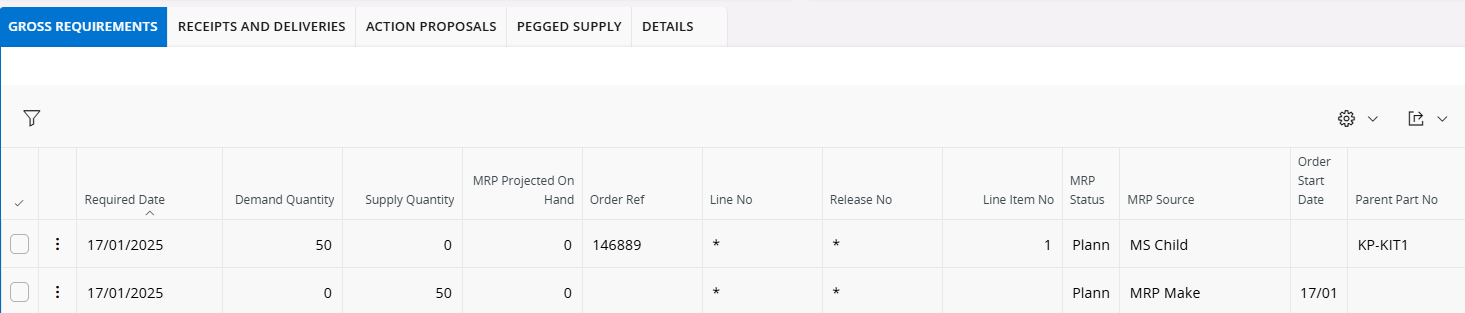
MRP Top Down Page - Gross Requirements for component:
Demand from MRP Explosion / Supply Requisition generated
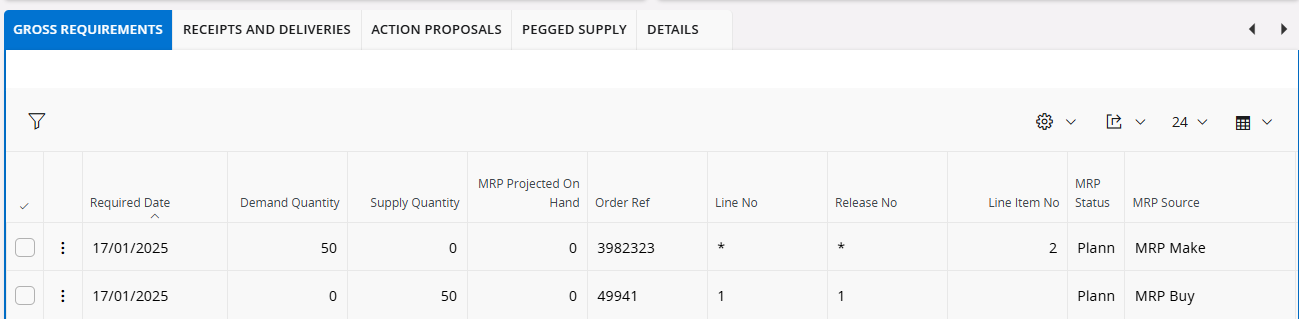