As of now Dangerous Goods, Classification, and Basic data are placed in HCM. Health and Safety. This is correct and it mainly discusses handling those materials from Health and safety perspective.
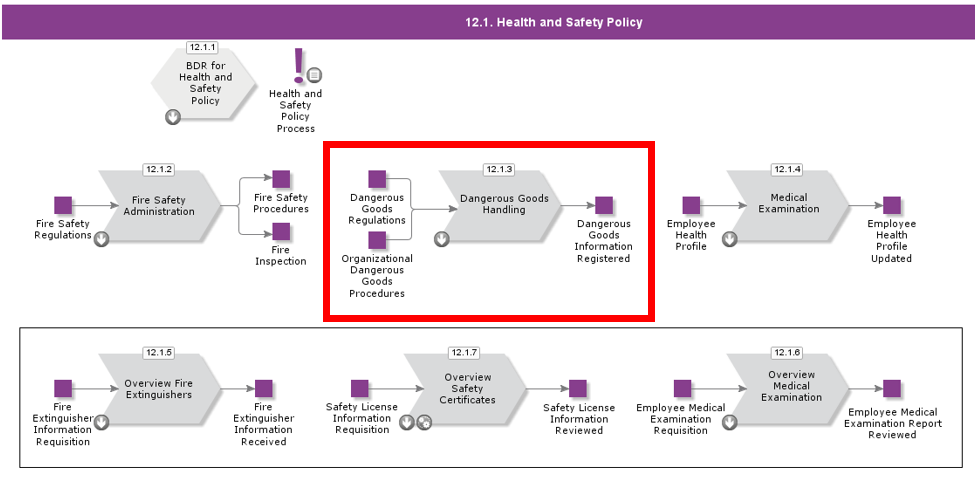
MSDS (Material Safety Data Sheet) information can be registered under Dangerous Goods Information.
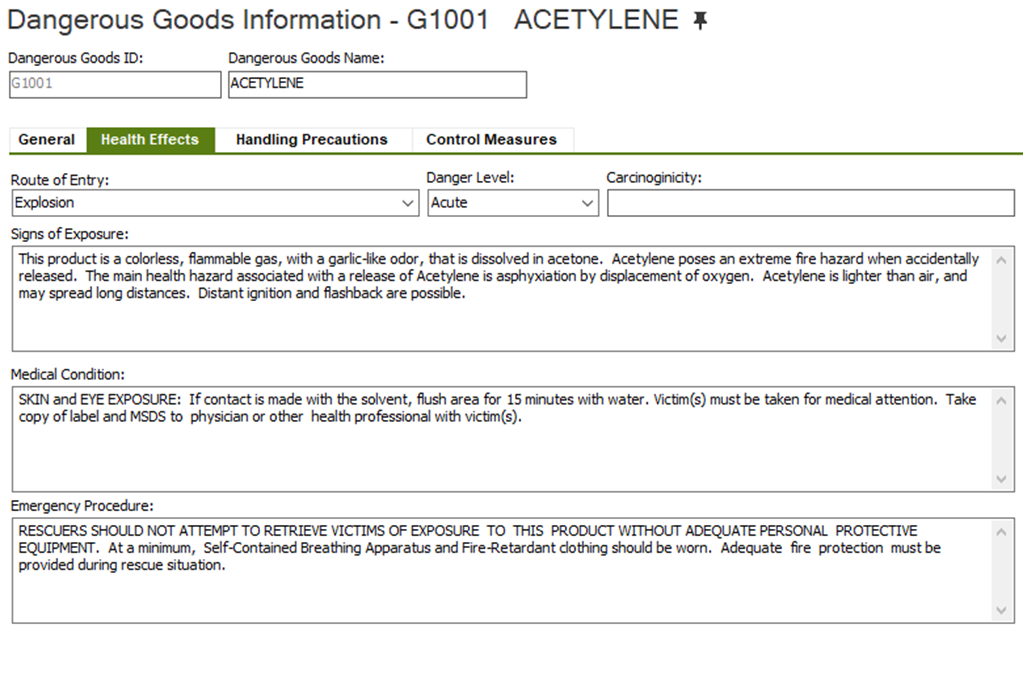
However, this information can be visible in Part Catalog as well.
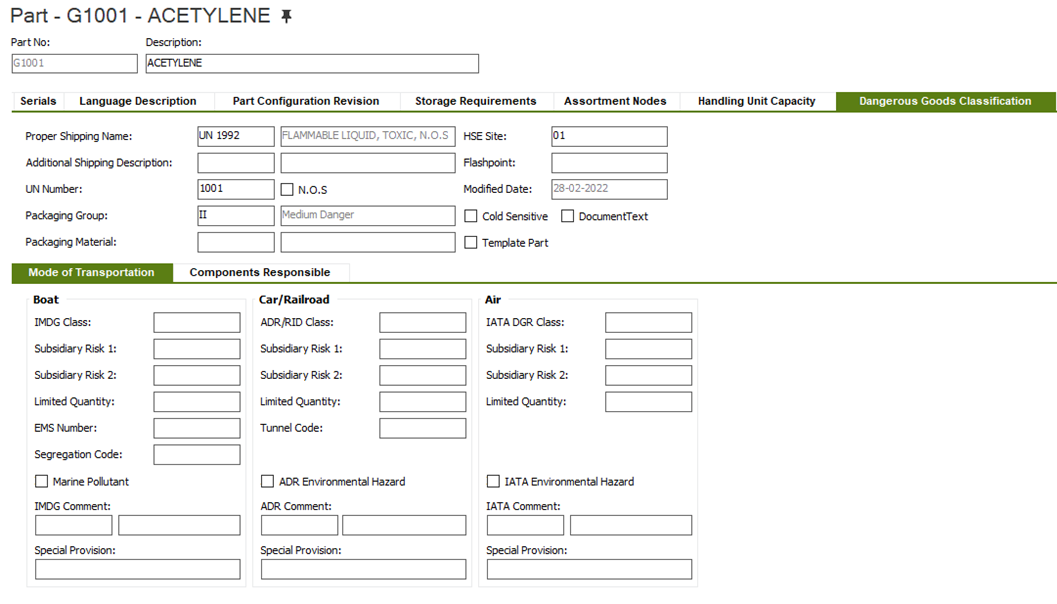
We have a few questions.
- How HCM/ Dangerous Goods Information connects with Part Catalog in SCM.
- As Part Catalog has shipping and packing-related information and how it will connect with IFS SCM Shipping functionality.
This is relavant to HCM and SCM.
Best Regards,
Thushan.