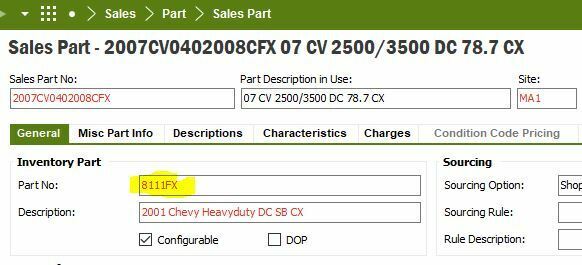
Can you Change Sales Part number to point to different Inventory Part? We want to keep the sales part number but it needs to point to a different Inventory part, is this possible or do we have to create a new sales part number? Transactions already exist. what are my options?
Thank you,