Hello,
We are trying to figure out if the following scenario is “as intended” IFS behavior:
Question: What’s the “correct” way to source INVENTORY parts for my WO when Inv Part in Stock =0?
Scenario: Test with 0 in stock (MMR = Maintenance Material Req.):
- Enter Inv P/N xx on WO/Req..s Tab/Part Req. Lines Tab -- Save (sys auto-adds an MMR line), -- leave Pur.Req. in Planned
- Release MMR header
- Run MRP.
MRP creates Pur.Req. for MMR line seemingly ignoring the WO tied (planned) Pur.Req. supply.
This creates an over-supply for xx. Is this as intended behavior?
Thanks.
Here's the over-supplied P/N xx :
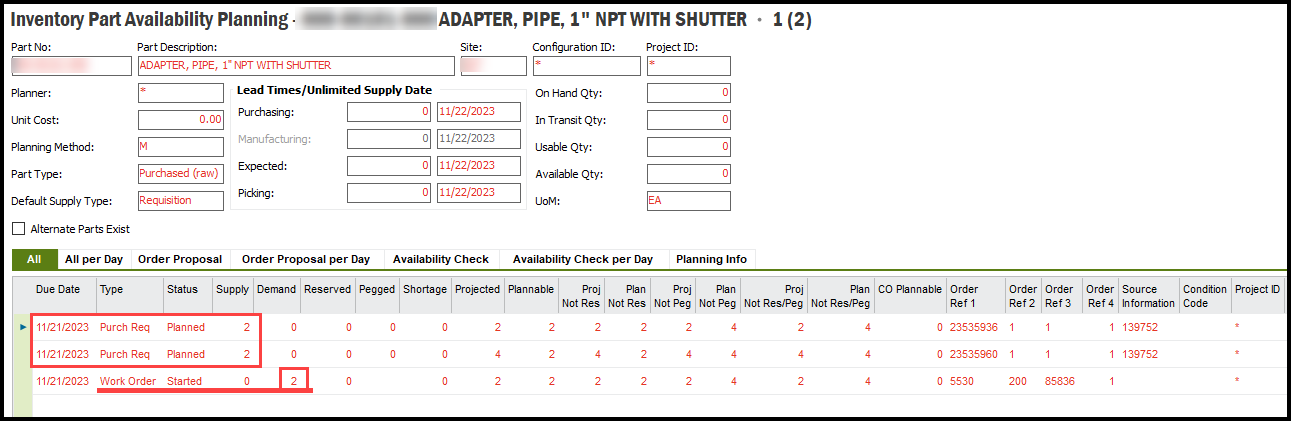