Hello,
I'm currently experiencing an issue in IFS Applications where the Kanban module shows stockouts (empty bins) on our assembly lines, even though materials are physically available at the point of use.
As a result, the main warehouse receives unnecessary pick requests, which show up on their picking lists, even though the items are already at the line.
In practice, warehouse staff often ignore these picks because they recognize the items as Kanban-managed — but this leads to confusion and inconsistency, particularly for new employees who aren’t familiar with the workaround. And sometimes there is also empty bins.
Additionally, we don’t use the Kanban card functionality when performing part movements — instead, we rely on manual transfers.
Could this be contributing to the issue? Could reporting delays (feel like this would lead to the opposite) or incorrect process flows be involved?
From my analysis, around 46% of where the system use the material from is from our main warehouse, despite material being available on the line.
One clear issue I’ve noticed is that our Kanban circuits is too small — but I’m wondering: Could that alone explain this behavior, or are there other factors we should consider?
Could it be that we use the set up wrong?
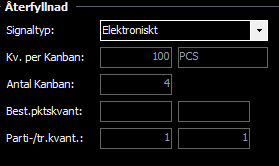