We are currently trying to use the order cover time on a manufactured part by setting it to Planning Method G. We want the demand as seen on MS Level 1 to be assessed over the cover time and used to generate shop order requisitions for the demand within the order cover time.
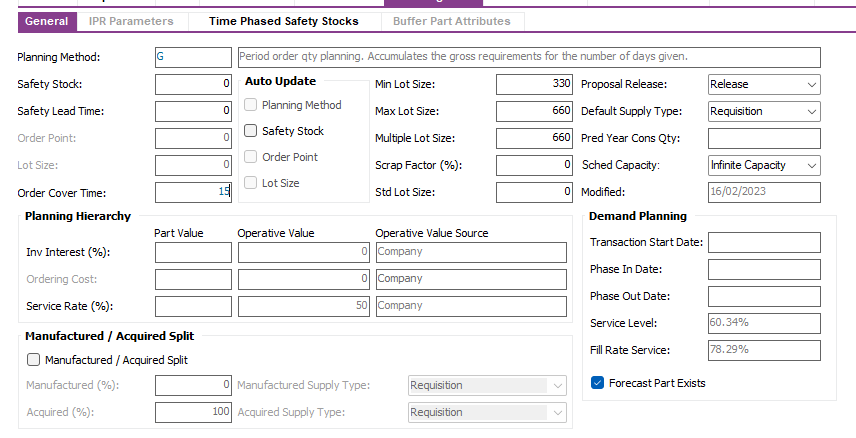
However, Planning Method G only appears to work for Purchased Parts. Has anyone managed to get this work for manufactured parts?