How can i remove any stock left in In Transit?
What do you mean by remove? Are they stuck in transit for some reason without the ability to receive them to inventory? Normally you can receive the stock from transit to an inventory location using ‘Receive from Transit’ screen.
Use below screen to receive stock from transit.
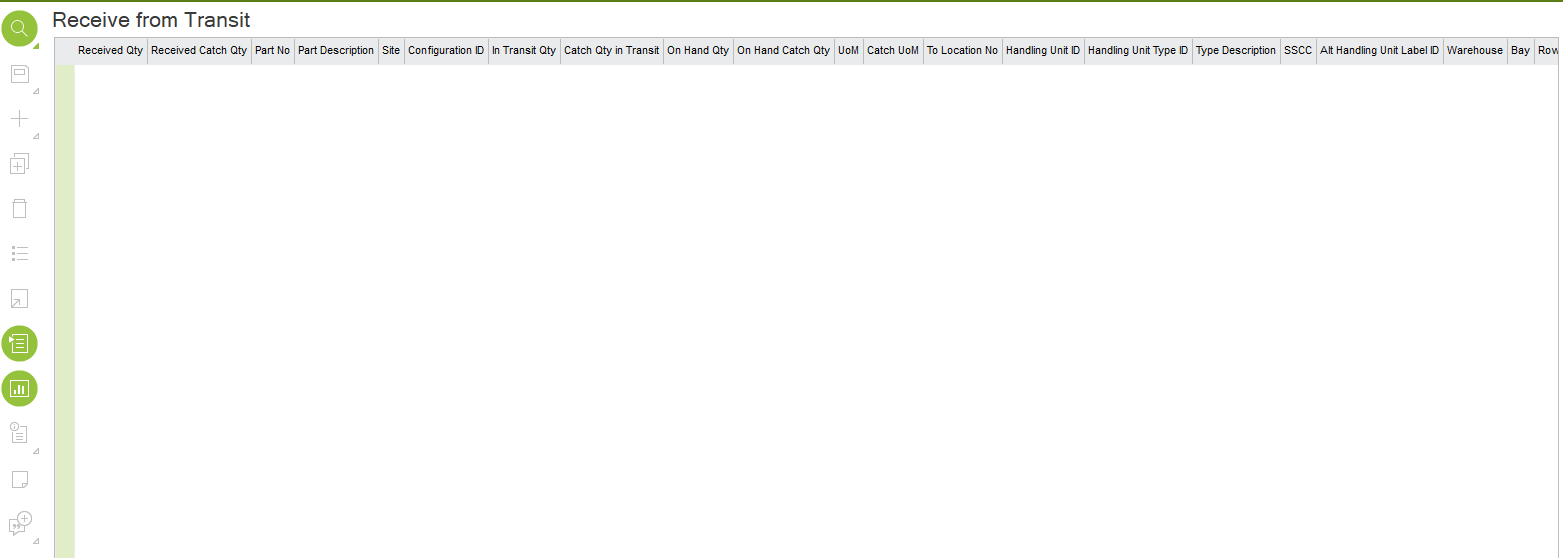
If you are referring to items that have become stuck in Inventory In Transit due to improper receiving of Intersite POs, the only way I’ve been able to clear that phantom material is to create another PO to do the receipt and then decide on which site the error occurred. I would then remove the resulting inventory from the site that messed it up in the first place - either scrap or issue to a project depending on how you want the transactions to go. I ended up getting a project from Finance for this purpose so they could see the impact.
I had to do this quite a bit when we first went live until the managers got beat up on the $80000 plus lost inventory, then it got quite a bit more disciplined.
If there are stocks in the ‘Internal Order Transit’, and there are no open Purchase Orders to receive the stocks against, what you can do is that, you can use Dummy Purchase Orders(s) to receive that stock. If you think these parts are no longer needed, you can Scrap the stocks once received at Demand end.
Actually, ‘Internal Transit’ and ‘Internal Order Transit’ are two different things, so ‘Receive from Transit’ is never an option to Receive an Stock from ‘Internal Order Transit’, whereas it can only be used to Receive Parts from ‘Internal Transit’ not ‘Internal Order Transit’ (Parts enters Internal Transit when you move them using Transport Tasks, or Move inventory using ‘In Transit’ option, not during Inter site Order flow). So, the only option here would be to create set of Dummy Purchase Orders and receive the stock against them.
To receive the stocks upon a Dummy Purchase Order, the steps you need to follow is as below,
- Get the Site (This is the Demand Site), Delivering Site (This is the Supply Site), Part Number and Quantity from Query - Inventory Parts in Internal Order Transit window.
- Find the Internal Supplier (s) connected to Delivering Site (s)
- Create a Purchase Order Header (s) for that Internal Supplier (s) in Demand Site
- Add Part Order Lines for above Part, Quantity combinations
- Release the Order(s)
- Query these Order (s) in Register Purchase Order Arrivals screen and use RMB Receive from Internal Order Transit option (In newer IFS versions, In transit option is available in Receipt dialog itself)
- Now you’ll see the Inventory Part In Internal Order Transit records in question. Include them in the Receipt
- Receive the Stock to a Picking Location
If you think this as excess stock, you can Scrap/Count out the Parts. Otherwise, you can use/consume the stock as normal.
Expanding on the original question, I always had trouble on understanding the best practices for the following scenario.
- Stock is moved from Location A to B via Transport Task / Move Inventory using “In Transit” Function. Lets say a quantity of 10.
- If Location B does not physically get 10 (things got lost half way while transportation) they got only 8 units.
How can this be handled?
- If the store person in Location B enters qty of 8 in “Receive from Transit” screen and receive only 8, what would you do with the remaining 2 which will sit in transit forever?
- Store person in Location B does not want to receive 10 and scrap 2 as it reflects on him and not the transportation.
- Store person in Location B does not want to receive 10 and scrap 2...
By selecting an appropriate ”Scrap Cause” and by adding a explanatory “Note”, he can clearly state that the Stock getting scrapped was something Lost during Transportation. That will then reflect in the Transaction histories, etc.. so it won’t reflect on him, but the Transport Task personal, etc...
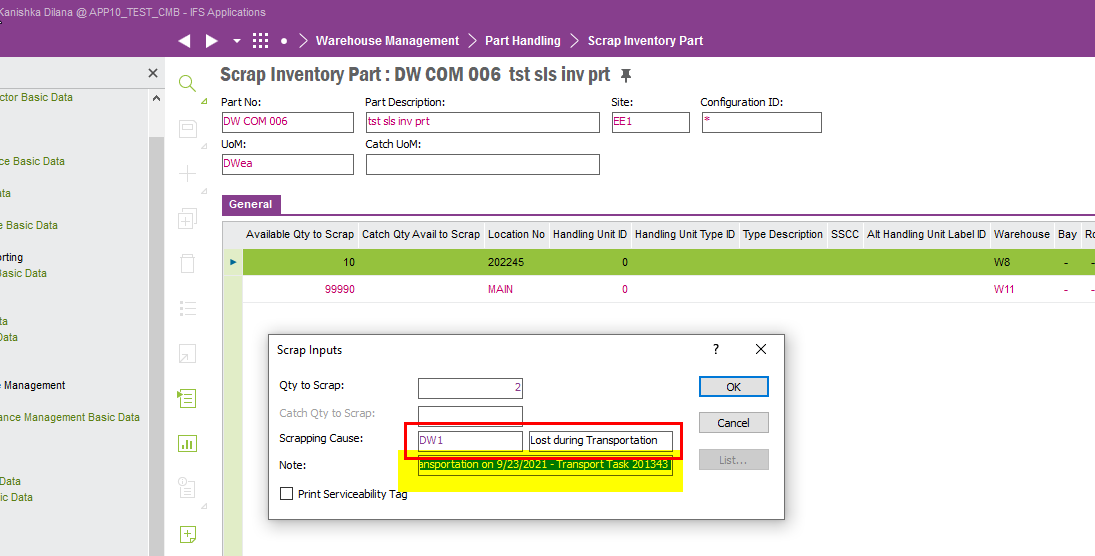
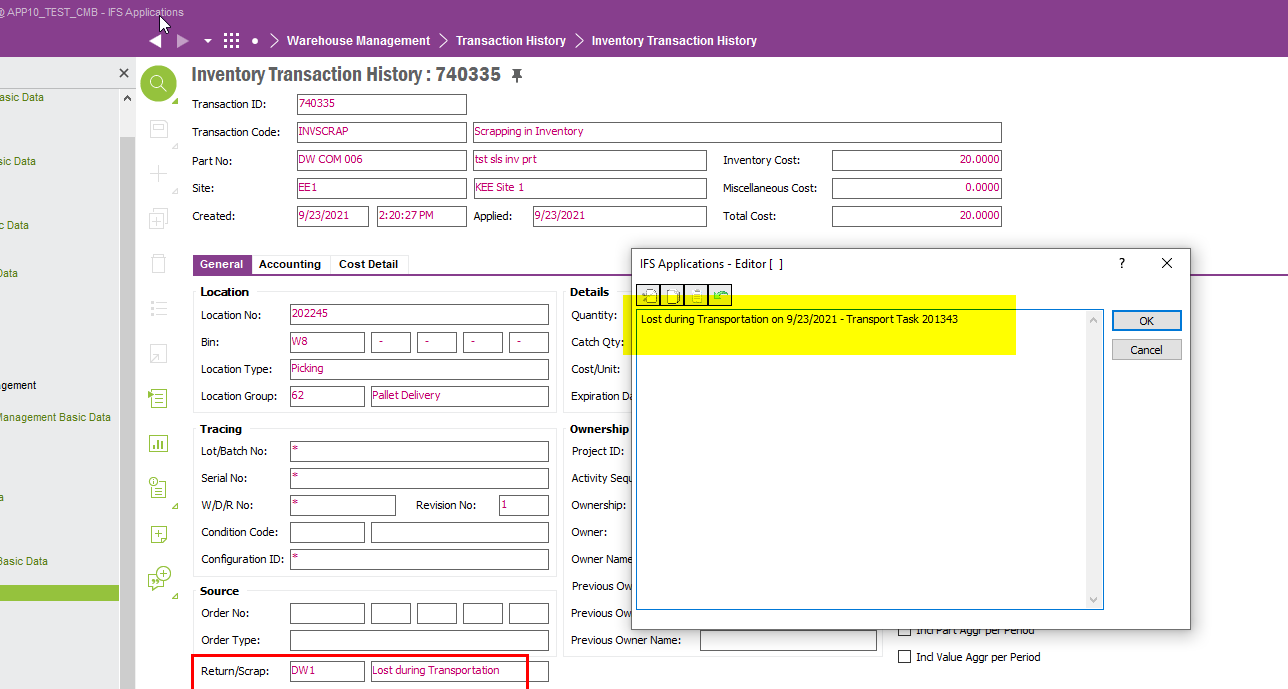
@Kanishka yes, Thanks! yes that is the process the customers are using currently. But when you run a report or analyse, what was sent and what was received at the other end is the same. Which is kind of not ideal. This becomes a big sticking point for warehouse staff, as they at times are adamant saying they did not receive the full qty and why would they want to record the total receipt . I know we can’t solve this, but thought of throwing the question to see whether there are any other options.
Yes, this will add an additional Moving step (I.e. You should first move the Parts into Truck, Perform whatever the Transactions to record the so called ‘Lost’ event, then Out of Truck at the Destination).However, given your requirement (You need to Trace exactly how Stock went missing, etc..) that will be the Best option I should say.
Here are the steps,
- Define a Remote Warehouse as follows,
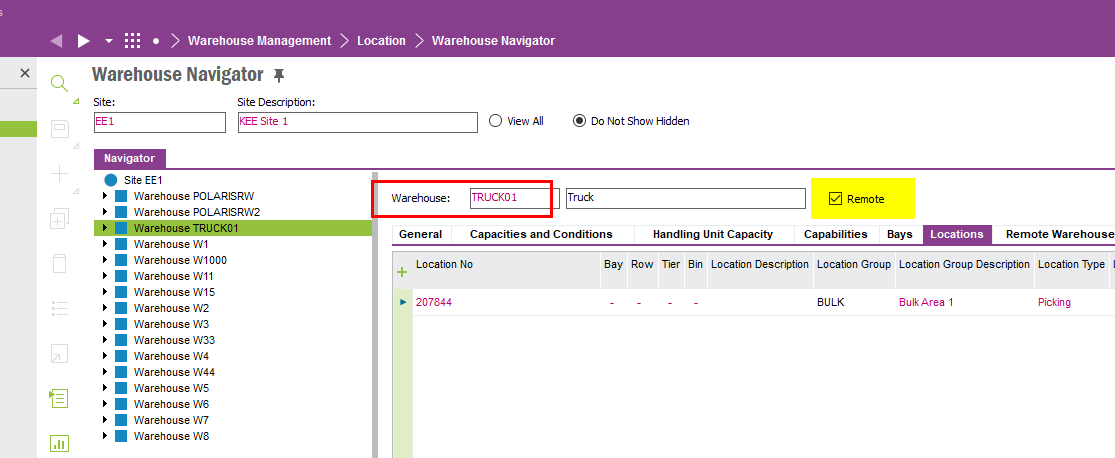
- Move Parts first into a Location within the Remote Warehouse (When you attach Locations to Remote Warehouse (RW), you should select the Location type as appropriate. Since we are expecting to Count out/Scrap Parts, you can select a Picking type Location for your RW). You can use Direct Stock movement option in doing so (“Move Stock” or “Transport Tasks”).
- If any items are Lost during Transportation, Count them out/Scrap Parts while stock is still in the RW.
- Move Parts to the Destination Location from RW. Again, you can use Direct Stock movement option in doing so.
I was having an issue with part stuck in internal transit as well. Happy to say the method mentioned above worked!
Thank you.
Reply
Enter your E-mail address. We'll send you an e-mail with instructions to reset your password.