Hi,
I have some questions / issues regarding PMRP. I hope someone could comment it or give me advice.
Or maybe also someone from IFS could determine if these are bugs and should be fixed.
Customer has reported recently negative projected quantity in Inventory Part Availability Planning after PMRP run.
After further analysis we have found, that it was due to shop order receipt during PMRP execution.
Below is the screenshot from TEST after recreaction of such situation.
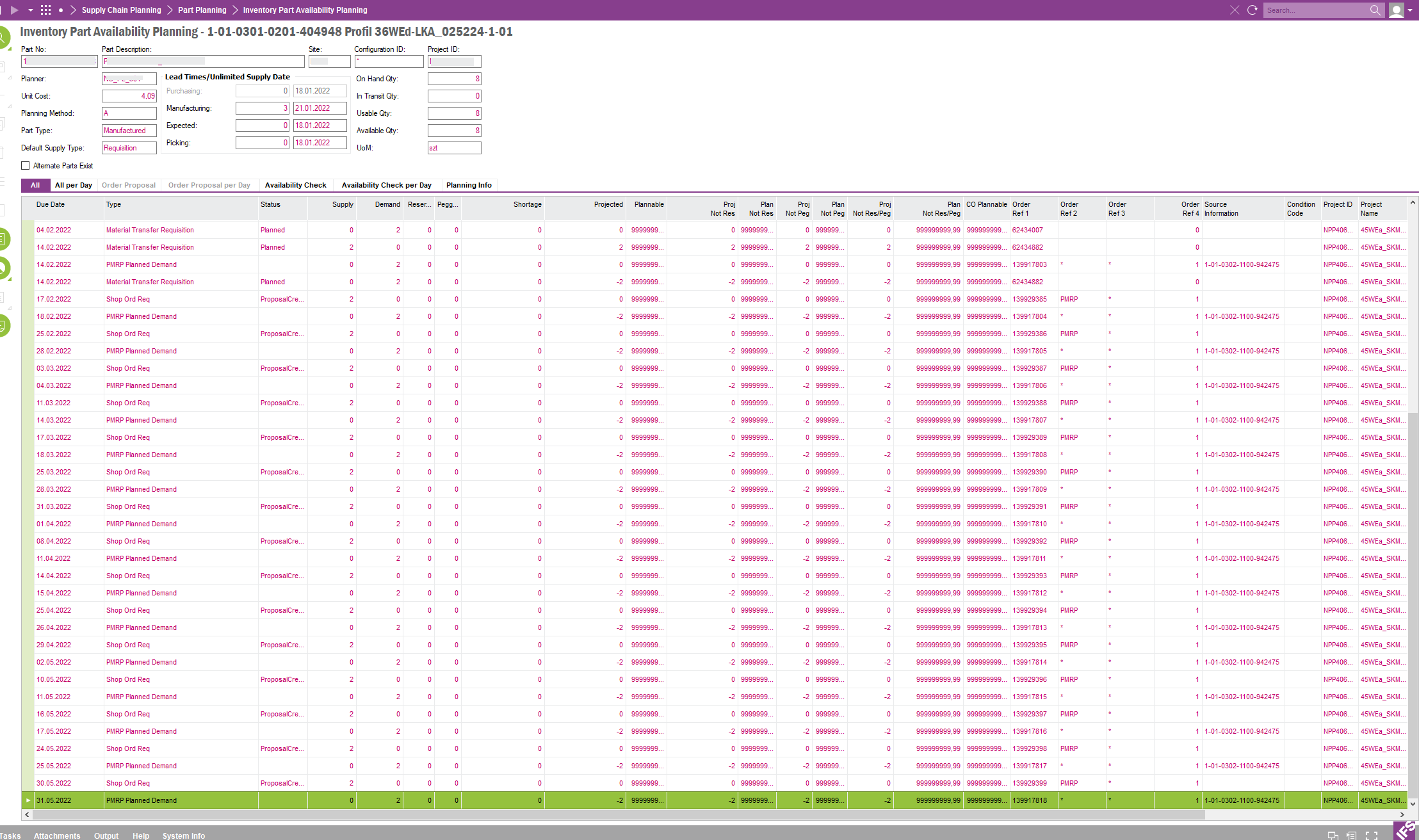
As you can see below in Pmrp_Plan_Snapshot_Api there are snapshots created one by one
And when you receive shop order during Snapshot_Shop_Order__ and before Snapshot_Inventory__ it will lead to situation when quantities from shop_orders are not match to inventory ones.
Due to heavy data volume, snapshot of shop orders takes approx. 10 minutes. So there is a big chance, that someone will receive shop orders during that time.
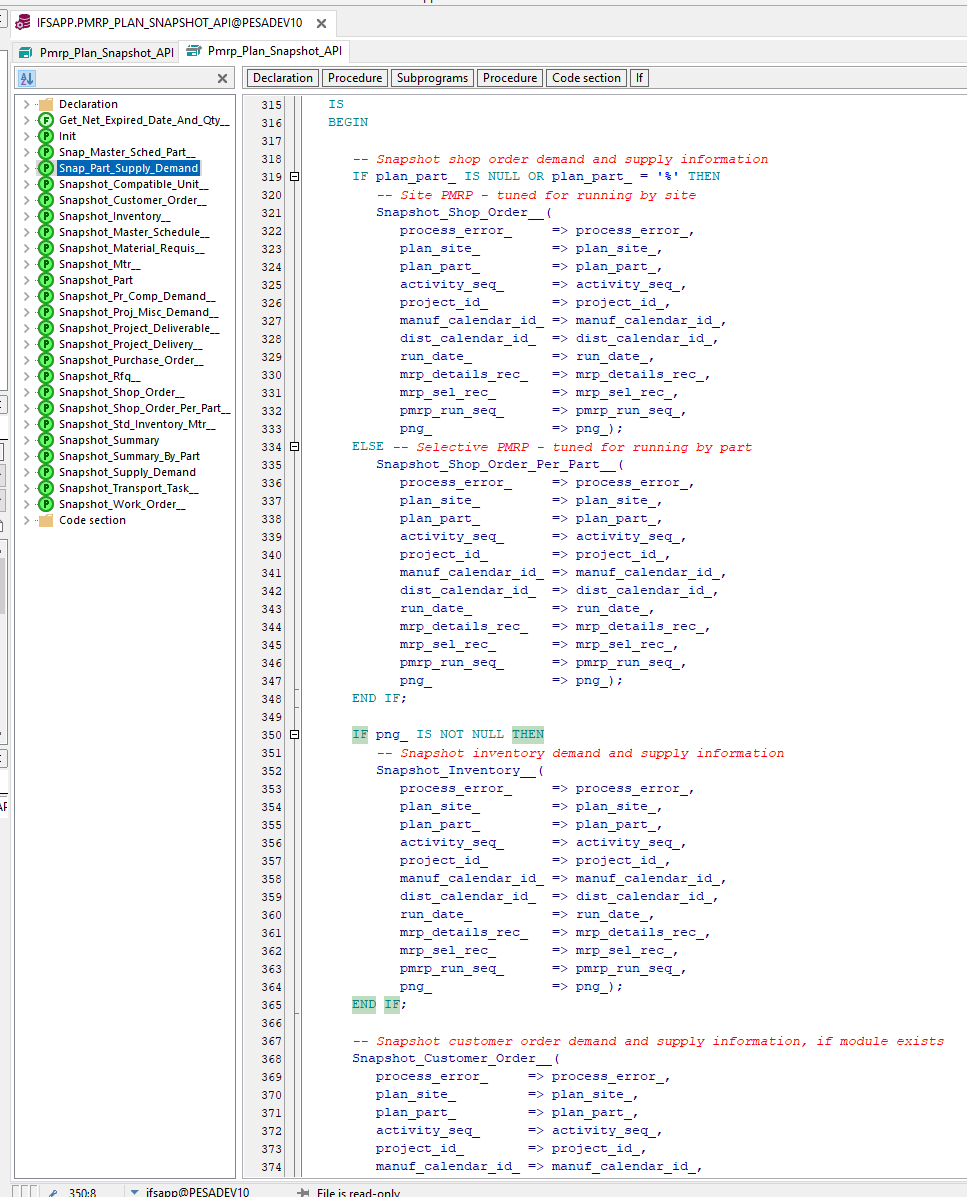
Customer company is working 24hr/day, 7 day a week. PMRP is being executed daily, usually at evening, but there are many PMRP schedules for many projects. It's impossible to find an hour or two to provide no inventory transactions.
How to handle such situation? It's impossible to check every part after PMRP. There is no information in such case, that something has changed during process and result for part XXX may be wrong.
And a suplementary issue found during analysis - we've found it during work order snapshot.
There was an information in background job, that for order XXX the date was not found in calendar.
It's a situation like below, when Required Date is null.
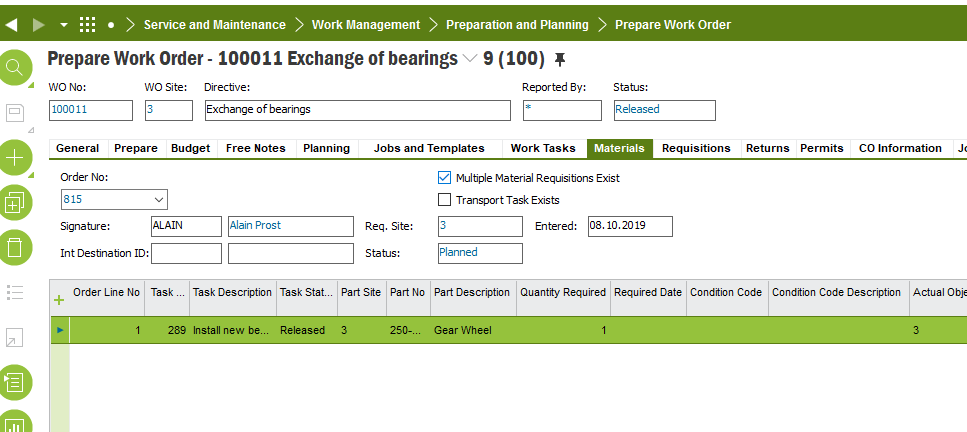
But in Snaphot_Work_Order__ in loop if something goes wrong, the error will be logged in exception and the procedure will end.
The same code construction is being used for other snapshots.
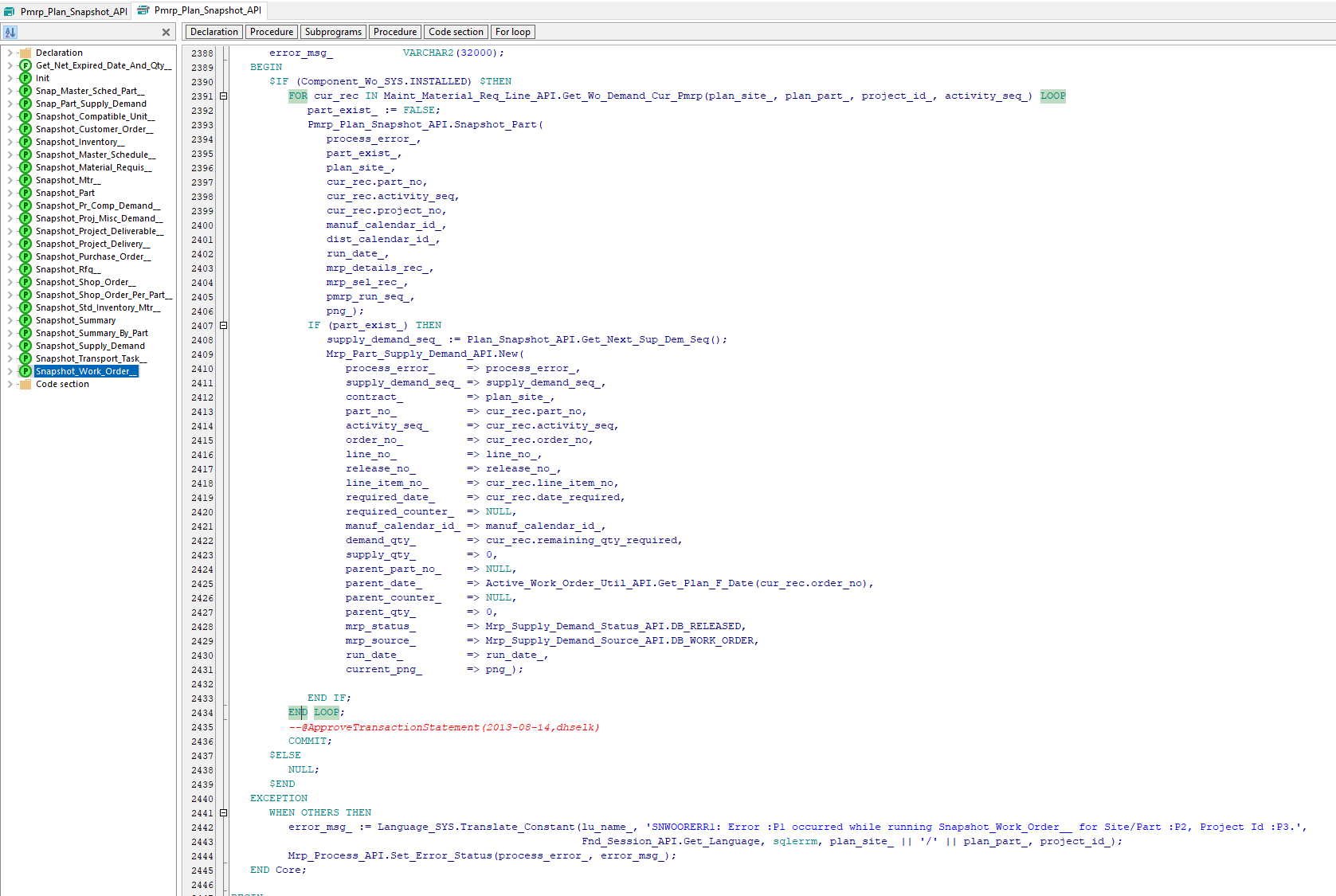
So when you have bad luck and there will be a problem logged by exception, the rest of the loop will not be processed.
I think it should be fixed in standard.
Best regards,
Hubert