Hello everyone,
While using the tool Shop order multilevel material availability i noticed the column (Minimum simulated start date) first i thought it represents the latest date where you can place the order taking into account the lead time (purchasing or manufacturing)
But while running the simulation, i had this:
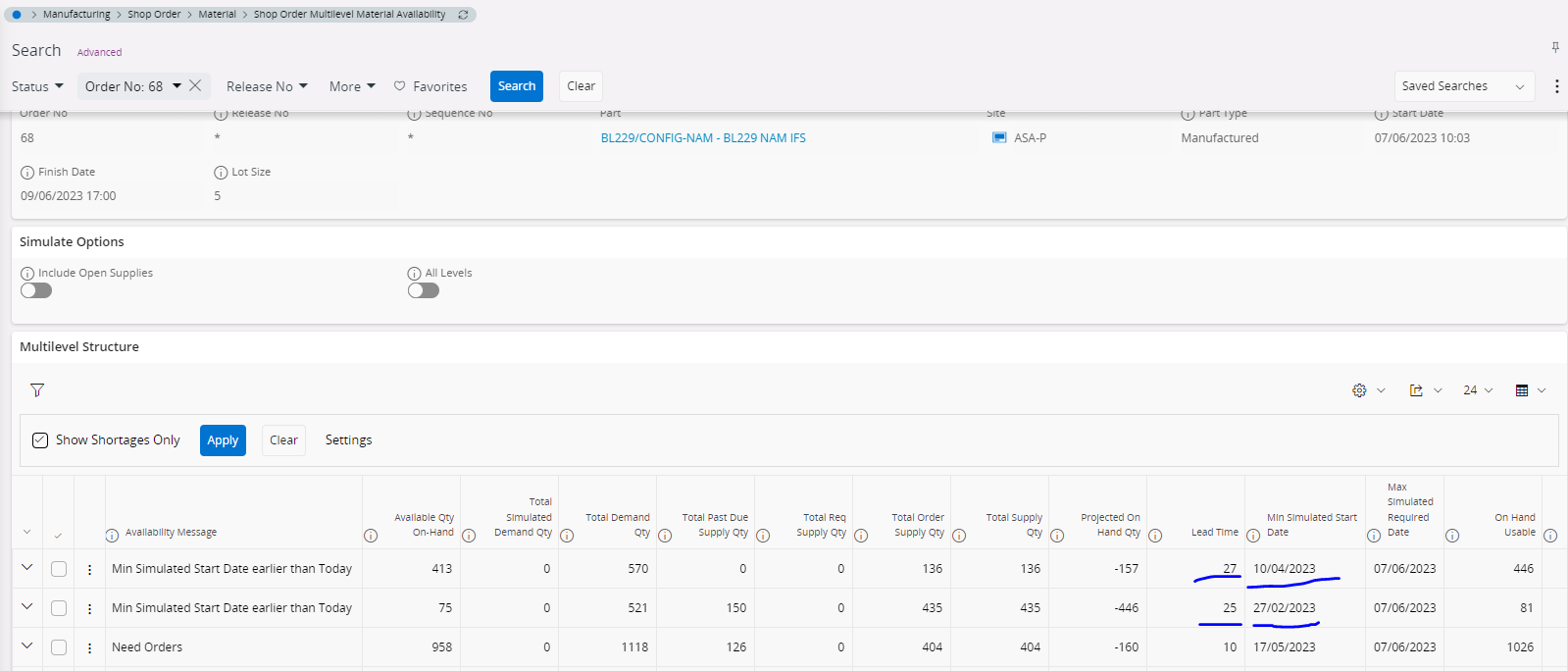
running date : 13 april
The system gives me minimum simulation dates in the past which is wierd because even if you take the lead time into account the date will still be not in the past.
Is somone familiar with this problem or might have another difinition of the minimum simulation date!
Thank you in advance