We are on IFS 10. We have historically been an ETO business and used engineered parts and projects. We are working to launch some CTO offerings where we will use the configurator and potentially DOP. DOP seems to be the recommended process when using the configurator. There are some strong opinions of DOP within our group, both positive and negative. We don’t want to have purchase orders pegged, but it would be great to have shop orders pegged. What is the best way to go about accomplishing that without having to manually set pegging preferences for each line on a DOP structure?
Hi
You have full control on creating “Shop Orders” or “Purchase orders” with DOP automatically/manually.
If you want DOP to open a “Purchase Order-Shop Order” for a specific inventory part, you will have to set your inventory_part’s default supply type = “DOP”
If your inventory part’s supply type is different than DOP, system won’t create any pegged requisition or order.
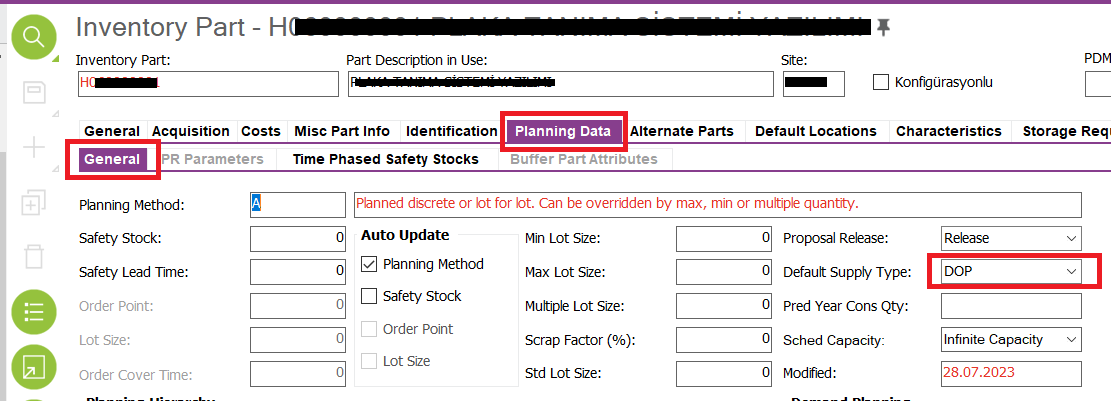
Thanks Ozgun!
I have a follow up - If we have some manufactured components that feed into the top level BOM, and if those parts are set as DOP supplied, how does that effect us if those same components are needed/used on a non DOP order? Some of our manufactured parts will be used in our CTO lines and also in our more customized ETO systems. We don’t plan to use DOP on the ETO systems and instead already use projects for those. So I’m wondering how having something set as DOP supply type would effect using that part in a project connected order with no DOP?
Hello
Sorry for the late answer.
Actually you need to analyze your own processes very carefully then you should choose your path.
My strategy with using DOP in our manufacturing was;
1- If we manufacture a part just because of a customer order, then the part is DOP supplied for us. (Doesen’t matter top level part or middle level part in the BOM)
2-If we manufacture a part independently from our customers, then the part IS NOT DOP controlled. We use MRP for this parts.
For example:
A customer want us to manufacture a bicycle which we doesen’t want to keep stock in our warehouse (just manufacturing and selling the product because there could be millions of configuration ID) for example 3 wheel bicycle. Then this bicycle inventory part is DOP supplied for us. So we manufacture and sell it.
But imagine the wheels are same for all configuration possibilities. Manufacturing and keeping in our stock 1000 wheels is much profitable. So whenever we have a customer order with bicycle we can use this wheels for every configuration possibilities.
That means wheels are not DOP supplied for us. We always want to see some wheels in our stock everytime and this process controlled with MRP.
For short, if we keep a part in stock then it is not DOP supplied, the other parts are all DOP controlled for us. Because all our finished products are tailor made for our customers.
And for your question;
You can a little bit bend the system for your needs.
You can let DOP to create structure for only the top level part, and open shop order for only top level part. And you can manage the parts manually which feeds top level part. But this process needs taking care of someone and to be done carefully.
Hope it helps
Özgün Bal
Thanks Ozgun. Appreciate the follow up and your response is as expected. I understand the nuances of how the different parts should be setup in a DOP environment. I think our situation is tricky because some internal stakeholders do not want to use DOP for all orders (i.e. not for the ETO orders).
We will continue to investigate our options.
Reply
Enter your E-mail address. We'll send you an e-mail with instructions to reset your password.