Hi, I have a site that make heavily configurable parts. They have separate part codes for each configuration. Slight variations. On the odd occasion they want to swap the part at the end to another part code on the shop order.
This works when adding parts. Receive it in, issue it to the next one and add the additional parts to the material list.
So they dont lose reported labour they want to receive the part into stock and issue it to another shop order effectively swapping the part number. However receiving the original part on the original shop order into inventory has risk as they have unissued some component parts and what they are receiving into stock isnt really what it says it is a parts removed.
Would you receive it in using W/D/R or condition codes to highlight the fact that it does not conform to the the part received? or cancel all the shop order and start again, would be shame to lose all the labour reporting in cancelling.
Question
Condition Code vs W/D/R or something else
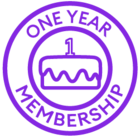
Reply
Enter your E-mail address. We'll send you an e-mail with instructions to reset your password.