Does anyone know the reasons why/when/how parts are moved to Internal Order Transit?
See Inventory Transaction Code INTORDTR - Move to Internal Order Transit due to issue. Those types of transactions cannot be traced back to a specific order because they do not reference an order type or number.
Example:

Also, the parts in Internal Order Transit do not reference an order.
Example:
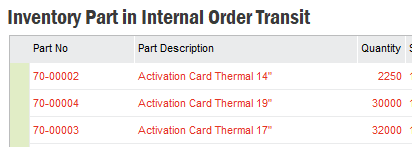