Hello all, the IFS Documentation shows this example:
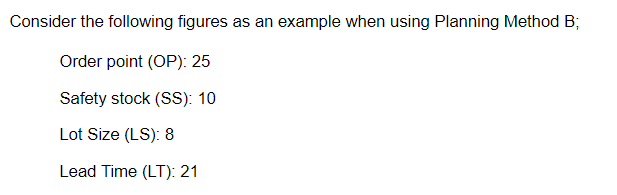
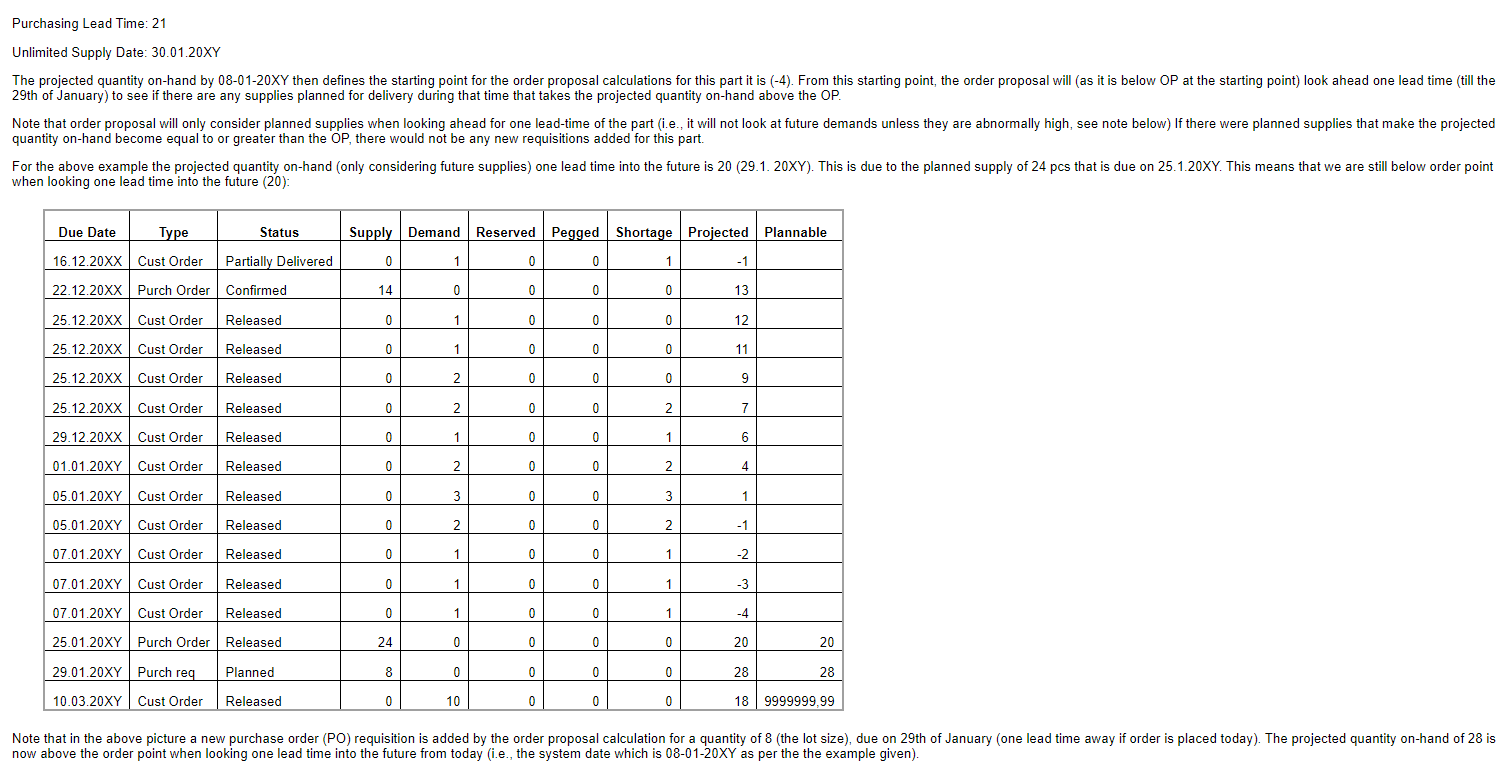
What would happen with Planning Method B if there is a demand within the purchase lead time period? For example a customer order reserving 10 inventory units on 26-01-20XY.
This would show a Customer Order in Status Reserved for 15 on 26-01-20XY, making the Projected QTY drop from 20 units on 25th to 10 units on the 26th.
My understanding for Planning Method B is IFS won’t “see” the future demand of 10 on the 26th and since the Projected Qty is still above the SS (SS=10 in this case), it will not trigger an Order Proposal for a purchase requisition of 16 units (2x 8 lot size) to buy now for arrival on 29.01.20XY. Am I correct?
If I am correct, why? I feel this means that if the daily demand for part keeps coming, they are at risk of being out of stock since IFS hasn’t created an order proposal foreseeing that we’ll be below the Order Point in the future.
I’m trying to understand in IFS Cloud how to manage inventory taking into account future demands we know are happening (reservations from stock or pegging from POs for future delivery)?