Hi All!
We runned into a Purchase Requisition with an duedate which we could not understand.
Hope someone in the community can help explain this.
It seems somehow that MRP is not creating an requisition with dueadate earlier than an already existing Purchase Order.
This is the scenario step by step:
We had an customer order(-5902), which was placed well ahead. And we ordered the parts for that order, also well ahead. (duedate 15-5-2024, And Purchase Order-57 was created, also duedate 15-05)
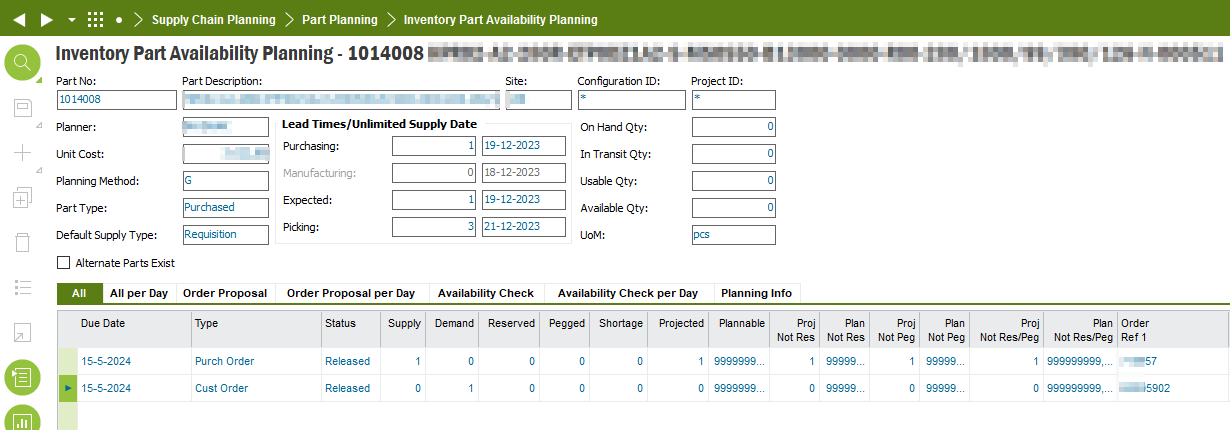
So far as expected
Later, another customer ordered the same part. (Customer order -5903)
This wanted date was before that ‘well ahead’order.’
(Duedate 13-02-2024)
The leadtime for the inventory part is 1 day.
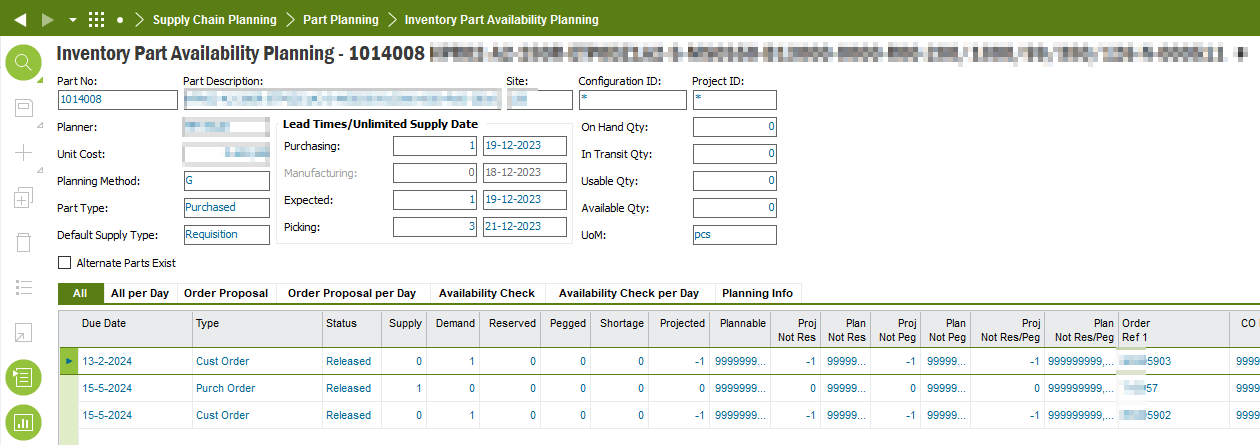
so far as expected
now we expected that running MRP will create an Purchase requisition with duedate 13-02-2024.
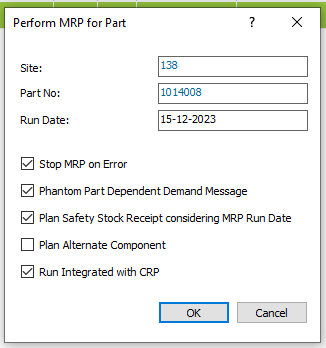
But.. an Purchase requisition with the same duedate as the other purchase order is created:
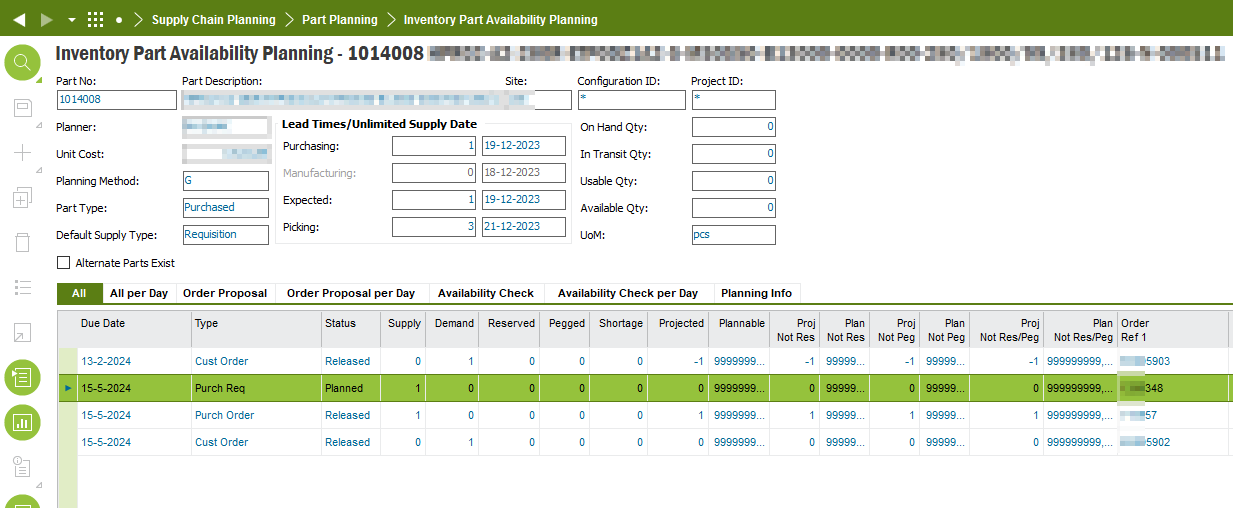
This is where i don't understand. Can someone help me why this requisition is not with duedate 13-02-2024?
order cover time = 5 days
MRP action proposals are also created:

Thanks in advance!