Has anyone tackled slitting metals using IFS, for creating setups/shop orders?
Can you elaborate a bit on the challenges you're facing with supporting the slitting process in IFS?
Can you elaborate a bit on the challenges you're facing with supporting the slitting process in IFS?
Bjorn, I am the solution architect for ClarkDietrich. They will take a large coil of steel and slit it into multiple coils of varying widths. The master coil is in pounds and the slit coils are in linear feet. We recommended that ClarkDietrich use individual shop orders for each slit coil width, each with differing quantity per amounts of pounds of master coil per linear foot of slit coil. We also recommended the use of operation blocks to group the individual shop orders on the shop floor workbench. One of ClarkDietrich’s concerns is how to track and allocate edge scrap (the amount of material on the edge of the rollers that is used to feed the master coil through the slitter). Another concern is the starting and stopping of the multiple shop orders from an operator’s standpoint. Other concerns revolve around setup instructions, etc. because the slitter is configured for the entire width of the master coil and not the individual slit coil shop orders.
Cappe can provide more details as necessary.
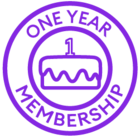
Nicely summarized, Vernon!
A few additional nuances that play in here are:
No real concerns in showing both footage and weight on masters and slits, as long as either could be used to drive MRP for determining raw and finished goods needs.
Width related - we sometimes take a “slice” of the coil and put the remaining back in inventory (taking some of the width of the master, but not all of it).
Length/Footage related - we cut/break the master coil lengthwise part way through the production (7 slits scheduled for the master, 2 “breaks” of the coil during the run, equals 21 slit coils, or 3 sets of 7 slit coils at varying footage/weight).
Total production for a master coil - ability to show that a 1000 ft master coil made 7 slit coils, each at ~1000 ft so what was 1000 ft available is now actually 7000 ft available, even though the total weight from master to slit (including scrap) hasn’t changed.
Old ERP handles these as one setup/shop order and shows all cuts, scrap, weight and footage.
Sounds like a good idea to have one shop order for each slit width and to use operation block to group all the shop orders that are going to be made from the same coil of steel.
Consider setting the slitting operation with a fixed resource share representing how much of the width of the coil that shop order will use to get a correct cost and load planning for that operation (since several operations will utilize the resource at the same time).
I would recommend to set the material lines for the coil with Reserve/Issue Method = Manual. Then you can put some scrap factor in addition to the QPA to count for the expected scrap planning wise. However, to make sure you actually consume one coil of steel (and the correct coil) for this set of shop orders you can select all these operations that belongs to the block in shop floor workbench and use “Issue Operation Material Manually”. In this dialog you can then specify that you issue one specific coil of steel to this block of operations. The quantity issued will then be distributed to the material lines according to their required quantity.
To clock time for these operations I think you should set the concurrent operations to “Allowed - Group Start in Parallel” on the work center. Then select all operations connected to the block and start the time. When done select the same and stop the time or approve operations. Time will then be split by calculating an actual resource share (how much of the resource an operation utilized during its duration). Each operation will receive the entire duration as the machine time value. (cost is machine time x resource share for the transaction). The actual resource share value is calculated based on the planned resource share (as I recommended to set on the routing) that should reflect how much of the coil width each shop order used.
Just some throughs on this:
Width related - we sometimes take a “slice” of the coil and put the remaining back in inventory (taking some of the width of the master, but not all of it).
I guess you use the function “Manual Unissue” materials already issued to at shop order. You cannot do that with a block. You will have to unissue a percentage of each slice one by one.
Also, you cannot scape from a block. That might not be a problem if your master coil is always the same widths. If not or you slit the slice you put back into inventory, you might have a challenge there (the scrape percentage will be higher).
Enter your username or e-mail address. We'll send you an e-mail with instructions to reset your password.