Hi, I am currently having trouble with shortage handling in IFS Cloud. I’m trying to get the shortage notification to appear when I place a Customer Order in the scenario where there is no stock available to fulfill the order. I have enabled the Shortage Notification toggle on the Inventory Part and the Shortage Handling toggle on the Parameters for Supply Chain and Manufacturing page. I have checked to make sure there was no quantity on hand and also see the orders with shortages on the Handle Customer Order Shortages page. Is there anything I’m missing for this message to appear? Any help is appreciated!
Hi Matt.
I believe the message appears when you are receiving material. I did the same set up and run the MRP and PR created for the CO demand.
And when receiving the PO via register arrival following message appears for you.
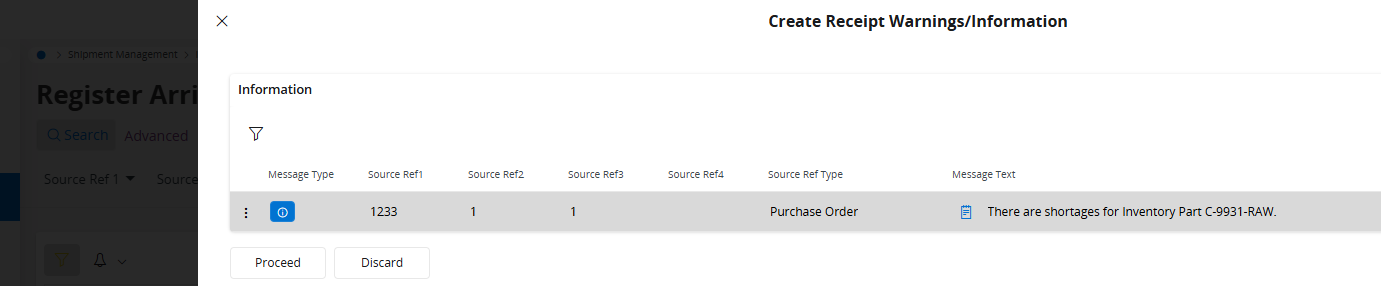
Thanks,
Chamath
Hi Chamanth,
Thanks for the reply! The part I am dealing with is manufactured and not purchased. I am mainly trying to see a notification appear at the CO screen when putting in the order of a part with shortage. Does this only work for the components that are being purchased? And I should be using either availability check or capability check to check for a parts availability/shortage with COs?
Thanks,
Matt
Shortage notification only shows up during the Arrival Registration process (i.e. what Chamath has laid out above).
IFS has a unique way of what it considers a “Shortage”. Records only populate on the ‘Handle Customer Order’ shortages page, if the material was attempted to be automatically reserved and subsequently failed.
It sounds like you just want the user to see that no material is available?
If so, you have a few different options but they can have many different impacts on your implementation:
- The Availability Quantity on the Customer Order Line will show you material that is Available in Inventory (although, this also shows Floor Stock inventory, which could potentially be confusing)
- If the part is a Make to Stock item, you could enable Availability Check which acts as an order promising engine in a way and will not allow you to overpromise. It can be useful, but some customers do not like it as it is sometimes a heavy handed approach. Lead-times need to be relatively stable for this to work effectively. This is not intended to be used with parts that have structures.
- If the part is a Make to Order item, then Capability Check is another option, but that is also a heavy handed approach. The structure can be evaluated and an alternative date can be suggested by the application, although, this check is being performed at a specific spot in time and capability can vary.
Honestly it can be a bit tricky to narrow it down as there are many variables. If you can share more about the product mix, turnaround, accuracy of lead-times and what the overall requirement from the customer is, it may be helpful for more of a concrete suggestion.
Reply
Enter your E-mail address. We'll send you an e-mail with instructions to reset your password.