We purchase labels on a spool of 25,000. Our supplier always adds an additional 500 labels (for good measure) to every spool but does not invoice us for these extra units. When receiving in the spools, is there a way to automatically “count-in” the additional 500 units so that the quantity on our handling units reflects what is actually on the spools? We don’t want to increase the quantity on our PO’s because we aren’t being invoiced for that full amount. We’ve considered using the inventory conversion factor and updating it to 1.02 but our finance department is worried about UOM conversions/reports/accounting entries as well as audits.
Hi
This is normally handled through Over delivery %, you may define Over delivery % as 0.021% ( higher than 0.02 which is 500 units out of 25000 ) and advise the system to generate a over-delivery alert, in case of exceeding 500, and accepting in case of below 500.
A warning message for equal to or less than 500 , and stoppage when exceeds 500. In case you want to allow higer %, you may update the numbers accordingly. This setup is on the PURCHASE PARTS
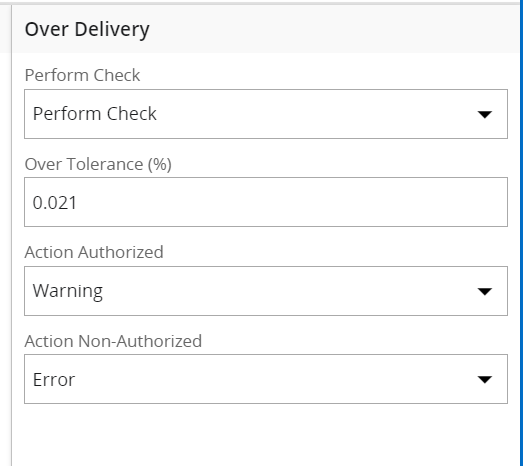
blank
Hello
Thank you for your input! Unfortunately, I don't believe this would add the additional 500 units into inventory. It just allows a receipt over the original quantity. We want to recieve just the original quantity of 25,000 on the PO because that is what we are invoiced for and then somehow automatically count in the additional 500 "extra and free" labels. We are looking for a recommendation on how best to achieve this.
Hello
I missed this thread and responding apologies.
Option 1 (recommended): Use PO change process, to add an additional line , with PO Price per unit as Zero. This will allow you to receive the additional quantity from the PO. The cost of the 500 units , if it is Standard cost, will follow the costing value, set previously. If it is weighted average then on receipt, system will recalculate the cost as per the weighted average (remaining qty on stock + 25000 + 500 ) will be used to average the inventory value. Use condition code, to mark as “Extra and Free” . If using Lot tracking, even that is an option to add lot id as “Xtra-Free-<PO_No-><date_stamp>”
Option 2 (Not recommended, but executable): Use the condition code, while counting In an extra 500, into the inventory. The challenge here is that this extra qty cannot be traced to supplier. In future if these create any challenge for warranty, or any supplier quality issues. Some manual intervention may also be needed, to manage the costing through re-valuation. f using Lot tracking, even that is an option to add lot id as “Xtra-Free-<PO_No-><date_stamp>”
Option 3: Enable the Over- delivery, with lot tracking and condition code as above. It is still feasible, but the receipt should be made a second time, to ensure 25000 is received in the first receipt with a different condition code (if needed) and Lot tracking (Optional) and then a second receipt for the over delivery by use of condition code, to mark as “Extra and Free” . If using Lot tracking, even that is an option to add lot id as “Xtra-Free-<PO_No-><date_stamp>”.
All three are to be TESTED in your test environment for net impact on the inventory costing .
Regards
Vivek
Hi
I understand you want to have the total of 25,500 labels but only pay for 25,000. Which at the same time means, the real unit price for each label is a little bit less than what you have in the order because you are receiving more labels.
If this is the case, you can just receive the total (25,500) using your normal receiving process. This will make you inventory qty increase in 25,500. In an hypothetical example where you buy each label at 1$, Inventory cost will temporary (depending on your costing method for that part) be increased in 25,500$ with a cost of 1$ each.
Then, when finance creates the Supplier invoice, they will enter the total invoice amount (25,000$), but match it against the receipt of you 25,500 labels. When the invoice is finally posted, your inventory cost will be adjusted with a reduction of 500$ and then you will have a total inventory cost of 25,000, with 25,500 labels in stock, at a unit cost of 0.98… approx each. Your AP account will still reflect 25,000$ and that’s what you will pay your supplier.
This is standard IFS functionality that depending on your costing method will create different transactions, but at the end, get to the same result.
In short, just receive the qty you are really receiving, and let AP do the adjustment at invoice entry to correct inventory cost and transactions that could be connected.
I hope this helps you.
Thank you,
Marcelo
Hi
I understand you want to have the total of 25,500 labels but only pay for 25,000. Which at the same time means, the real unit price for each label is a little bit less than what you have in the order because you are receiving more labels.
If this is the case, you can just receive the total (25,500) using your normal receiving process. This will make you inventory qty increase in 25,500. In an hypothetical example where you buy each label at 1$, Inventory cost will temporary (depending on your costing method for that part) be increased in 25,500$ with a cost of 1$ each.
Then, when finance creates the Supplier invoice, they will enter the total invoice amount (25,000$), but match it against the receipt of you 25,500 labels. When the invoice is finally posted, your inventory cost will be adjusted with a reduction of 500$ and then you will have a total inventory cost of 25,000, with 25,500 labels in stock, at a unit cost of 0.98… approx each. Your AP account will still reflect 25,000$ and that’s what you will pay your supplier.
This is standard IFS functionality that depending on your costing method will create different transactions, but at the end, get to the same result.
In short, just receive the qty you are really receiving, and let AP do the adjustment at invoice entry to correct inventory cost and transactions that could be connected.
I hope this helps you.
Thank you,
Marcelo
Reply
Enter your E-mail address. We'll send you an e-mail with instructions to reset your password.