Hello IFS Community!
In this workflow we have a 4-Level Intersite PO:
- What we call “the Order Desk” (L1)
- The Product Line in USA (L2)
- The Product Line in Canada (L3)
- The manufacturing facility (L4)
Going into the details as to why the PO matrix is structured that way would be going on a tangent, and to make this post as short as possible (is likely going to be long anyways as the problem is not easy to be described) I’m going to concentrate on our issue.
Take this PO for example (where you can see the 4 levels stacked up nicely in the Supply Chain Customer Order Analysis screen)
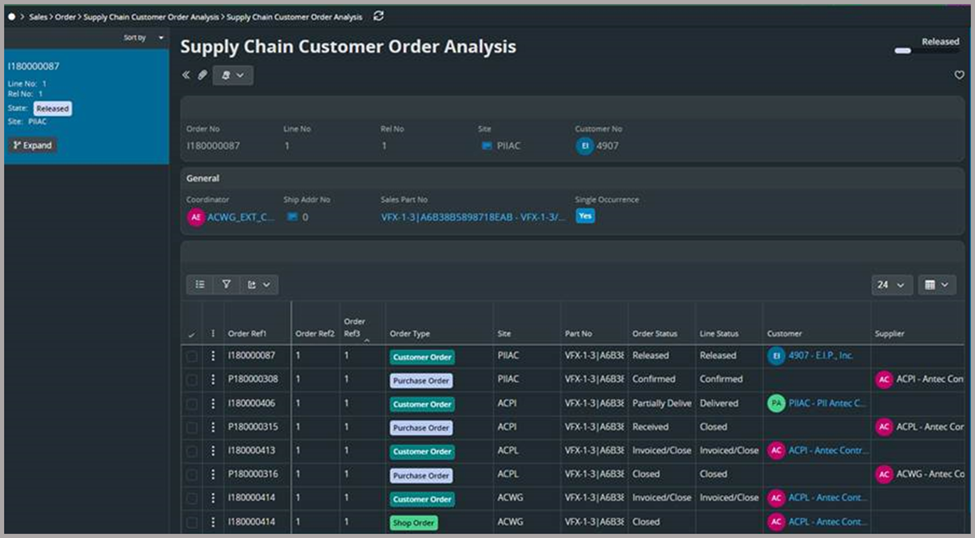
Our issue can be summed up like this: after releasing a L1 CO, IFS goes and automatically creates subsequent Level 2 CO and PO, Level 3 CO and PO and Level 4 CO and Shop Order (where the component really gets manufactured) for us. After that, eventually the work gets done, Shop Order is Closed, items are shipped to customer, the Level 4 CO Invoiced, etc, etc. So far so good.
And then the problem looms: in one (and only one) of the CO lines there seems to be a problem. The L2 Purchase Order (in this screen shot P180000315) stays in Received (does not Close) and one PO Line Status is stuck in “Released” (not “Closed”).
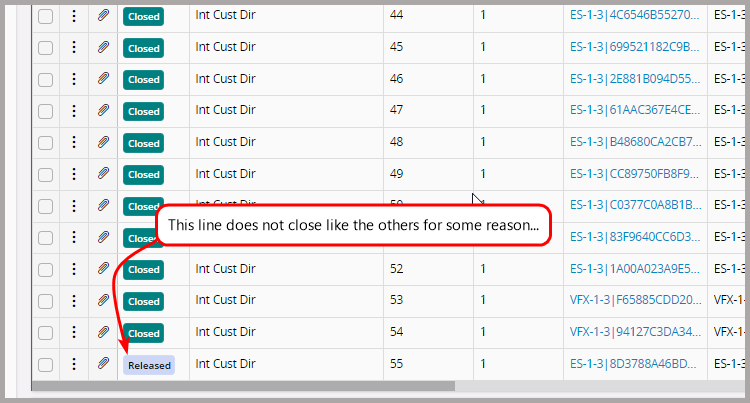
Attempting to register this arrival notes that the value of this line may not be 0 and it stays in the list.
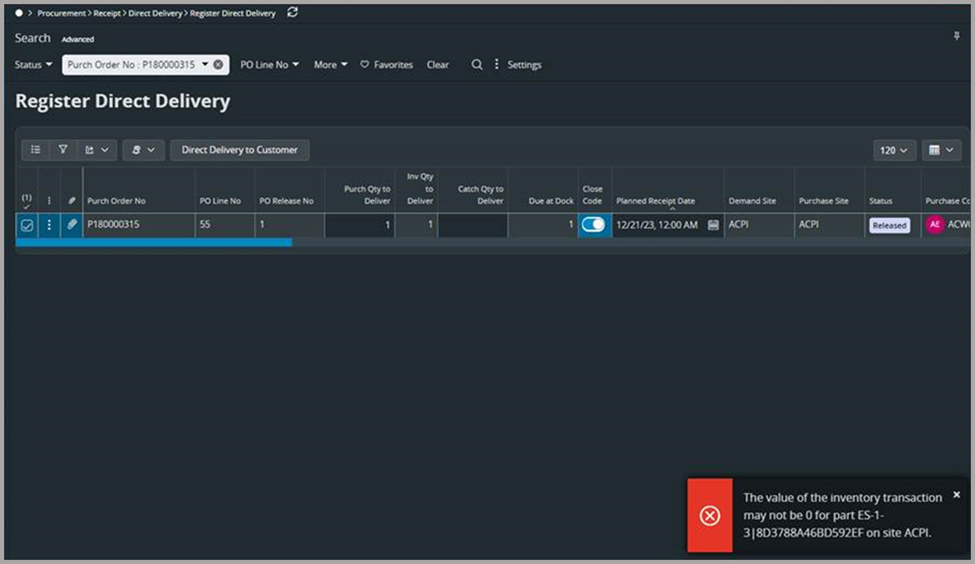
We believe there must be something wrong with this line’s part configuration (compared to the other 54 lines in the CO that makes it act the way it does). Here is how that line is different from the others:
Level 2 PO (P180000315) for that line has no Price...
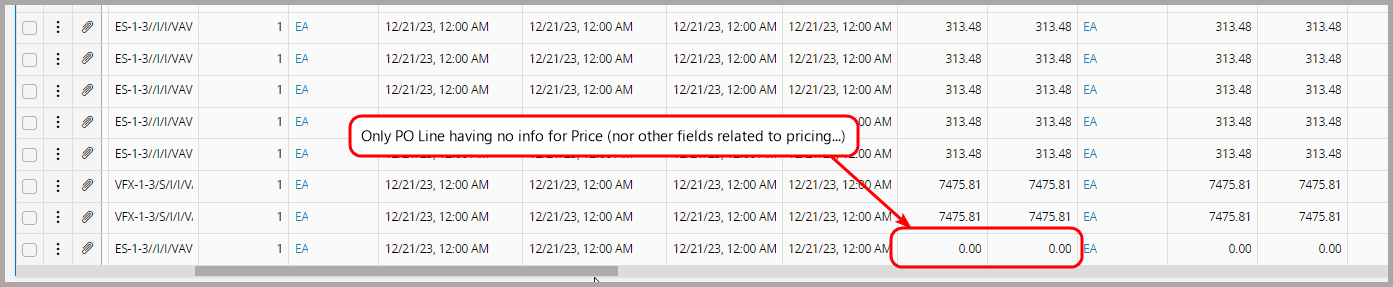
Level 2 for that CO also is the only line in that CO having no Cost for some reason
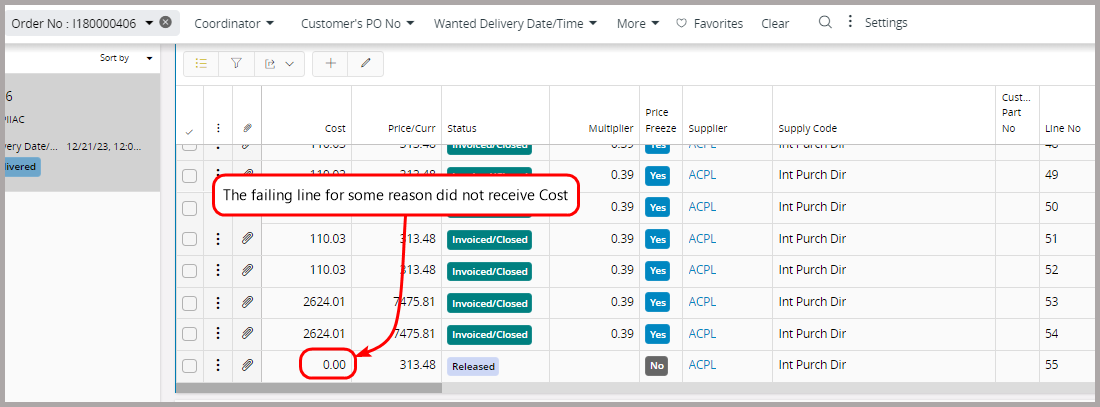
So the question is: what could be wrong on this line? could there be some miss-configuration on the Inventory/Sales Part that is preventing that specific line from receive the costing information from the bottom layers? what code in IFS populates the cost of a part when that part (on that site) has no cost and rather is manufactured further down the chain? how can I troubleshoot this in a way that can help me see what the root cause of this problem may be?
Any idea is appreciated!