Is it possible to move an inventory part to a Quality Assurance location if the part was not received on a PO? Manufacturing would like to move non-conforming parts to a non-conformance location until final disposition is determined.
The Location Type does have certain functions or limitations based on the type selected:
Location Type
Select a location type from the list box. There are twelve different location types:
Picking - used for storing frequently consumed purchased or manufactured parts. Pallet-handled parts moved to Picking Locations are converted into individuals.
Floor Stock - used for storing parts used in the manufacturing process. Locations of this type are intended to be controlled by IFS/Manufacturing.
Quality Assurance - used for thorough inspections of both new arrivals and stored parts with recurring quality inspections. Parts on this location type are not available for reservations. Locations of this type are intended to be controlled by IFS/Purchasing.
Pallet - used to store one pallet per location. Pallets in locations of this type are available for reservation for customer order but cannot be partially reserved. Pallets can be issued only via transport tasks and can be moved to both pallet and non-pallet locations.
Pallet Deep - used to store multiple (infinite) pallets in one location. Pallets in locations of this type are available for reservation for customer order but cannot be partially reserved. Pallets can be issued only via transport tasks and can be moved to both pallet and non-pallet locations.
Pallet Buffer - used for additional deep storage with infinite storage per location space. Pallets in locations of this type cannot be reserved.
Pallet Delivery - used to manually receive parts, not from a purchase order, and create pallets automatically. Parts in locations of this type cannot be reserved until moved into stock.
Shipment - used to combine several customer orders for more efficient handling, especially multiple orders on one transport vehicle. Issued and Packaged parts can be stored in a shipment location until shipped. Parts in locations of this type cannot be counted.
Production Line - used to connect to a specific unit in the manufacturing process. Locations of this type are intended to be controlled by IFS/Manufacturing.
Arrival - used to receive parts into a location controlled by IFS/Purchasing. Parts in locations of this type cannot be reserved but can be inspected.
Pallet Arrival - used to receive pallet-handled parts into a location controlled by IFS/Purchasing. In locations of this type, pallets will be created automatically but are not available until moved into stock. Quality inspection can be performed.
Pallet Quality - used for thorough inspections of both new arrivals and stored pallet parts with recurring quality inspections. Pallets in location of this type, controlled by IFS/Purchasing, cannot be reserved.
For us, the Quality Assurance Location Type is much too limiting - for exactly the scenario you describe. You would be better off to define a separate quality controlled warehouse and quality locations by function and control the inventory in that manner. Here is a view of our quality warehouse - all Picking type locations (the one Quality Assurance location we stopped using due to its limitations):
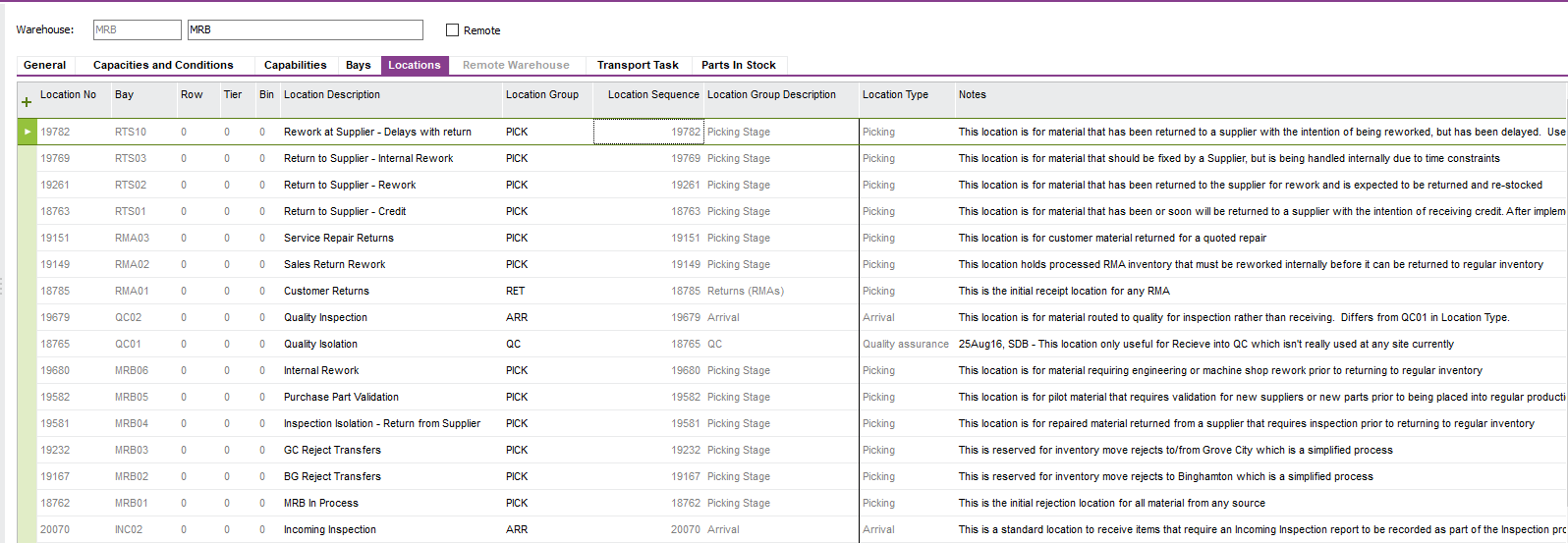
HI
I’m sorry, To move parts to a arrival or QA location, the move itself needs to be done in the context of the purchase order receipt (a receipt ref is needed for these location typed. So you need to find the record in PO receipt window, and then use move function on PO receipt to move to a QA location. If part is not at the latest picking location as identified on the PO receipts you first have to move it to that location. Hope this helps.
Further following link will be helpful for you :
Hi
You can define the most suitable receive case in the Supplier for Purchase Part which will satisfy the requirement.
According to your requirement, you may use anything other than Receive into Inventory. Then, once the PO arrival is registered, PO status will get the Arrived status and the PO Receipt will get the To Be Received (or To Be Inspected) status, until the QA inspection or Movement to Inventory location is done.
The receive case you define in the supplier for purchase part will be there in the relevant PO line also.
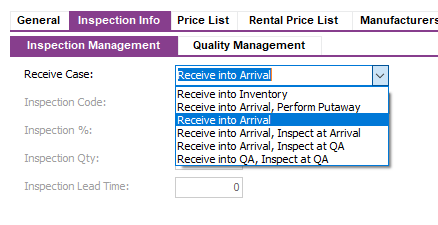

If an inspection is done, you have to define an Inspection Code as well in the Supplier for Purchase Part. You may use Inspect at QA or Inspect at Arrival based on the location types the site has.
Anyway, whatever the receive case is, an inventory transaction will be generated, since an arrival is done, but the PO cannot be closed until the Inspection is completed and the items are received into inventory (to a picking or floor stock location)
Thanks,
Enter your E-mail address. We'll send you an e-mail with instructions to reset your password.