Hi All,
I’ve been looking at a scenario where Master Scheduling is being used in conjunction with Order Gap time, but I’m struggling to understand the logic of how MPS is generated.
I’ve set up a simple example in my test environment (24R1) to demonstrate:
Max Lot size = 10
Order Gap Time = 1 (just to simplify - in reality this would be different hence why rate by period hasn’t be set up)
Test 1 - Works as I would expect - the MPS generation stops at the PTF, so the system cannot keep the Projected balance positive and an Action Message is generated.
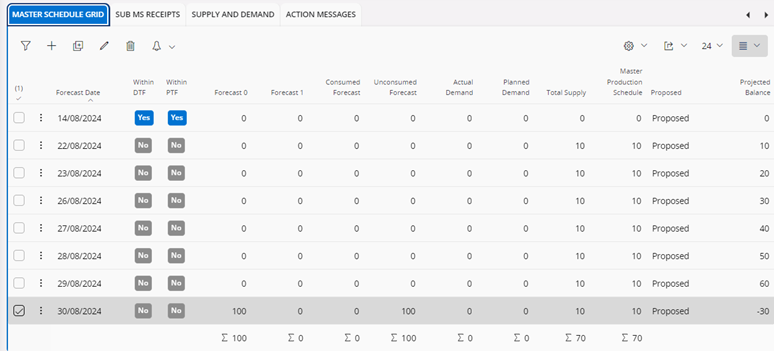
Test 2 - However, if I split the forecast into 2 overlapping periods, the Order Gap time rule is ignored and multiple MPS/SORs are generated on the same day and the project balance is now always at 0 or above.
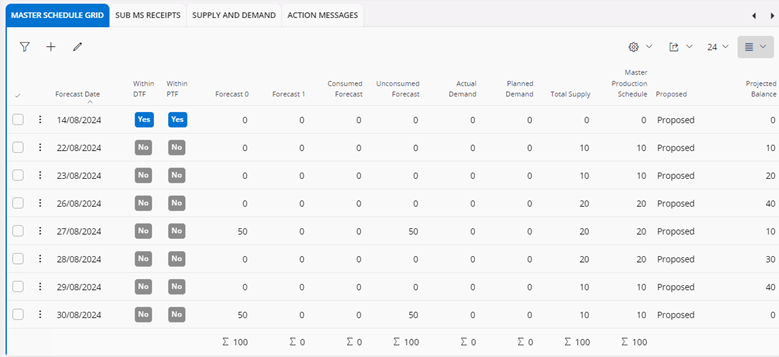
If I add a large forecast at the PTF, I get a strange pattern, I think where each demand entry (forecast) is searching back for a free day, hitting the PTF and creating one SOR for the max lot size. However the overlapping demands are not considered, so the order gap time is not followed.
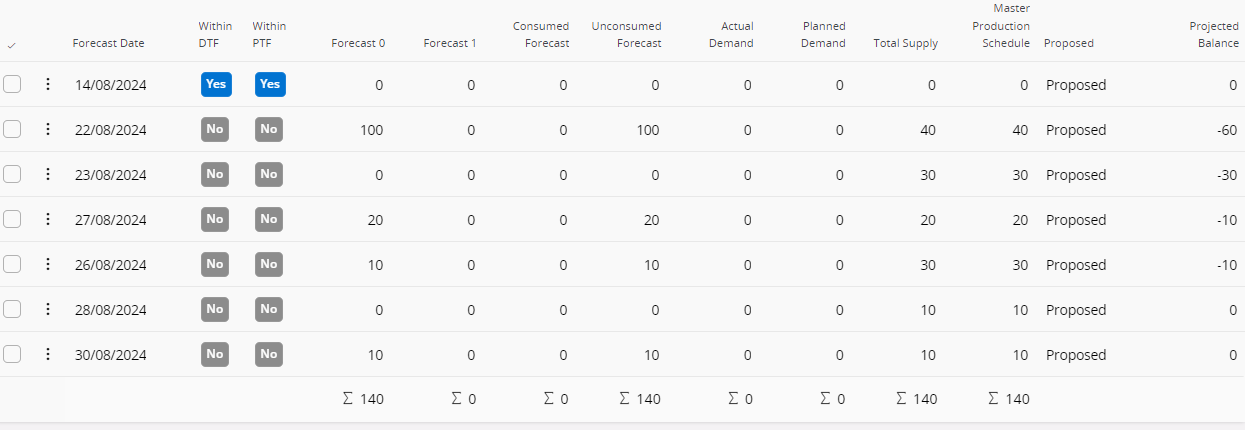
Is this intended system behavior? Or is there a logic that needs to be followed carefully when using order gap time and Master Scheduling?
Thanks in advance for any comments/ideas.