Hello,
We are looking to improve manufacturing cost estimates and cost reporting through IFS. We primarily design and fabricate custom systems with job-unique BOMs. We are not using DOP at the moment, but have it on the radar in the future. On the shop order costs page, we can see estimated and actual material, labor, machine, etc. costs. Until items are issued or operations are reported, the actual cost is $0. Thus, the estimated cost can be useful.
An issue with the estimated cost is that it is $0.00 for new items that don’t have a history in the system. Even once these new items are received into inventory and there is an inventory unit cost, the estimated material cost field on the Inventory Part Unit Cost page still shows $0. Thus, other than our interconnecting piping, fittings, etc. that are used on every job, our estimated cost is completely missing. We can add a CRIM to update the estimated material cost field after material receipt, but it seems that this field gets filled in automatically by the system at some point, and we don’t want conflicting processes working against each other.
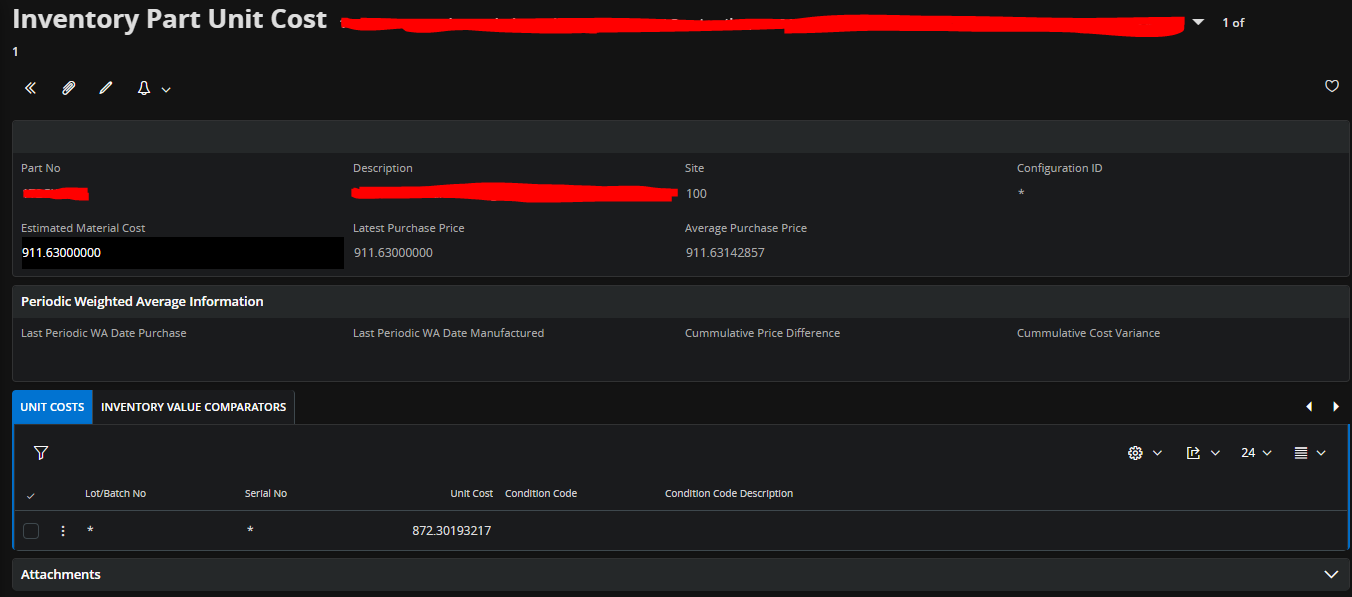
A few questions: How & when is data for this field generated out-of-the-box? Is there any way to configure it via basic data? How do others get accurate job cost estimates prior to having purchases received into inventory and issued to the job?
Thanks,
Dylan