Hi community,
Looking for your suggestions on the following.
One of IFS customer has raise their concern as the tracked structure solution in Shop Floor Workbench in IFS Cloud is not providing the needed support for them.
Their production is based on traceability (Lot/Batch or Serial No) and every product produced by the company is marked with product number and serial/lot batch. Therefore, getting a readable reference on the serials produced in a Shop Order is important to their production.
In IFS Cloud, scaling a Shop order in lot size or having a serial contain a lot of sub materials/assemblies has made the tracked structure unreadable to the customer.
Refer to the following screen capture from IFS Cloud,
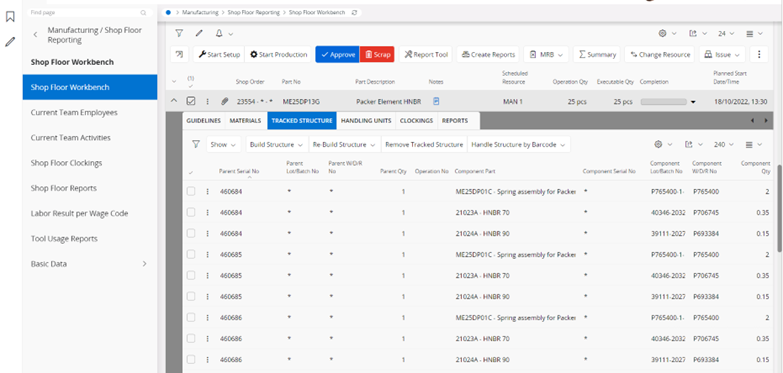
In order to get to the needed information in IFS Cloud they have to scroll down and marking 25 unique serials.
The customer requirement is to have the same capabilities as they had in Apps9 since it gives the following benefits to the customer
- Easy view the serials
- Improves the navigation for verifying the QA of the data, for example when you need to ensure the manually provided certificate matches the serial components in the main part serial.
- Easier to see the materials issued when continuing a production when there is a temporary production stop
Example from APP9;
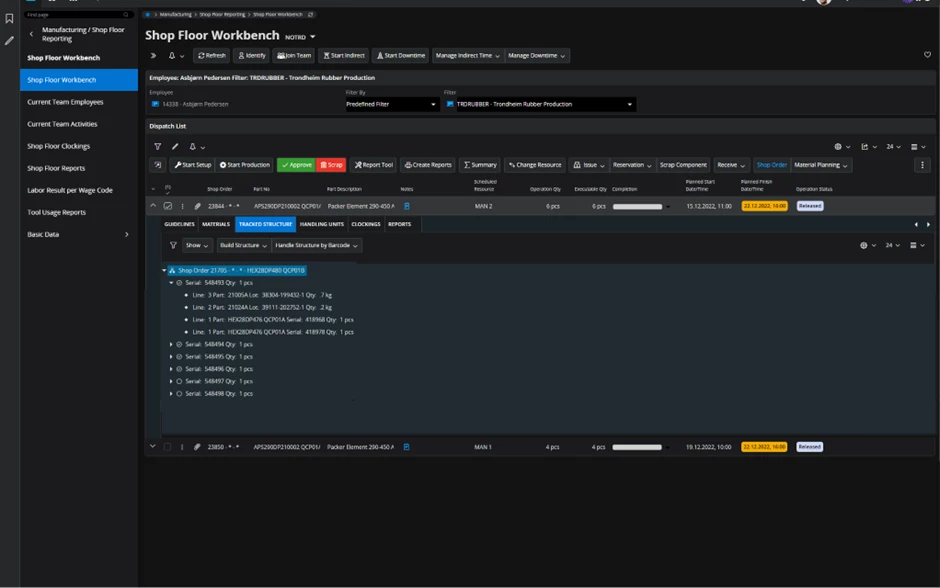
Thank you,
Nimesha