Hi Community
need advice on the best method/ practise to use to handle customer order that are required to be in stock but not being shipped until the customer is ready to receive them which is current an unknown due to various factors.
We still need to manufacture the parts in the sales quantities but as we are unable to ship the products we currently push the date out until the end of the following month. We have been doing this for several months and now have a customer order book which shows demand to manufacture and ship multiple customer order lines at the end of the month which invalidates the accuracy of the customer order book. (see below)
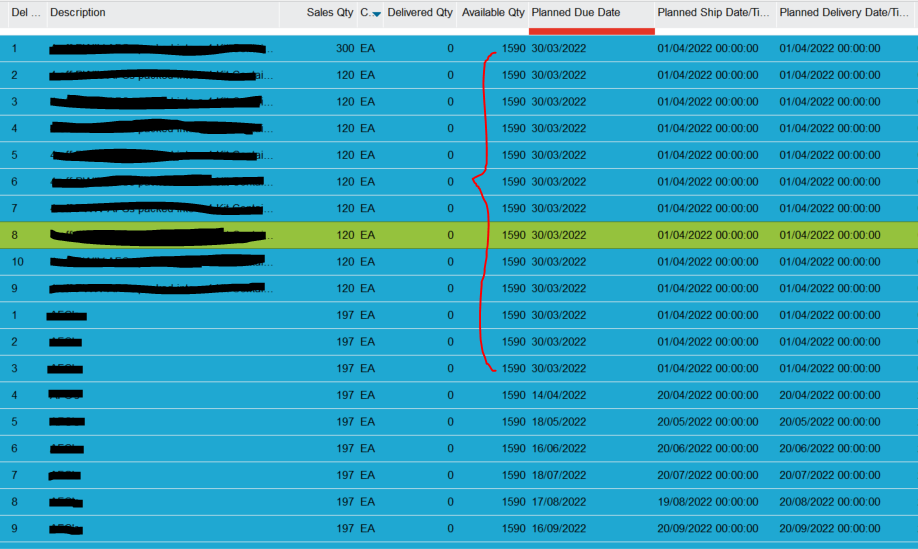
We are currently still invoicing monthly to the custom even though we are not shipping the products physically or on the system.
is there a better way we can handle this situation so we can ship the products on the system or move them to a holding location until we are ready to physically ship them?
regards
Jamie