Hi all,
if someone can help in explaining rules system applies in shop order costing and accounting records of stock as some figures are hard to reconcile. We use IFS APP10, run our manufactured products on Standard cost, Cost per lot batch. When we open new item, we would expect that Estimated cost from Shop order cost are used to record receipts of qty on stock prior shop order is closed. However, we see system using quite different numbers some time, and we can not reconcile them to any calculation of the cost.
Examples below:
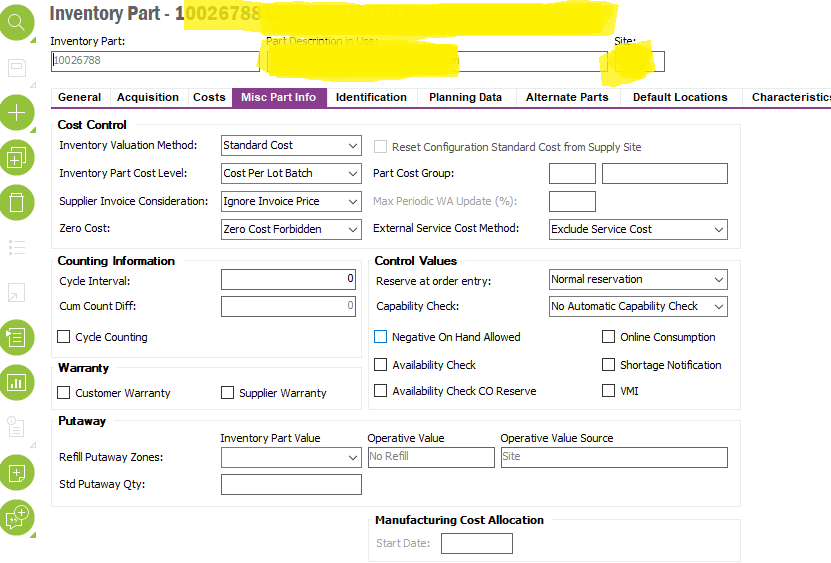
This is cost for same shop order which was reported in two steps. Cost per pcs of 3,67907 is one we would expect to be actual based on set up (machine and labor rates, material cost, etc.)

However, the first reported qty per shop order was at cost of 4,19 and estimate in Shop order cost was 5,01. Even weighted average cost of this part we are producing was not 4,19
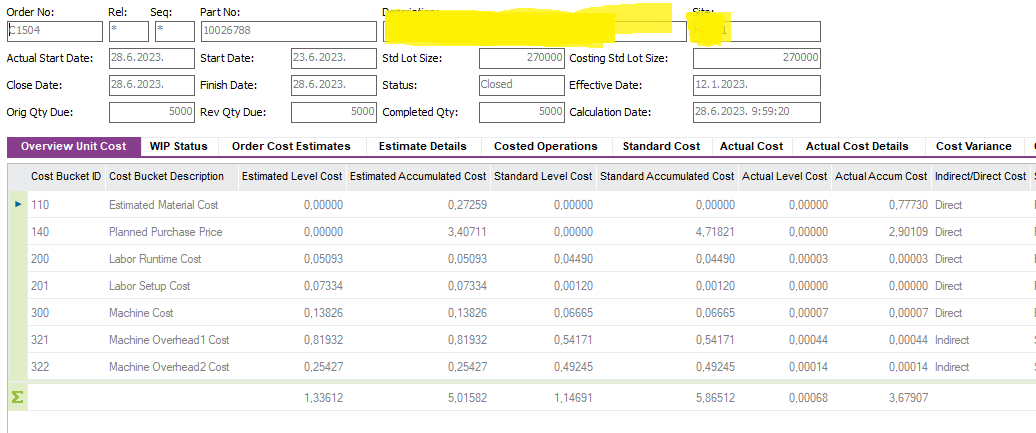
We see that system is using some figure to report item value on stock prior shop order is closed, and we can not reconcile it. Since we have long running orders of 100k pcs and more, with reporting handling unties that contain only e.g. 70 pcs, the positive and negative variances are sometimes quite big and we can’t explain it to our auditors.
Does someone know/have an idea where this number could come form, how system generates it, etc. that we could reconcile it.