Hi!
Question from a customer who is upgrading from APP9 to IFS Cloud. Is there a way to have the setting for Default Backflush ONLY to have affect in Shop Floor Workbench and NOT in Receive Shop Order manually?
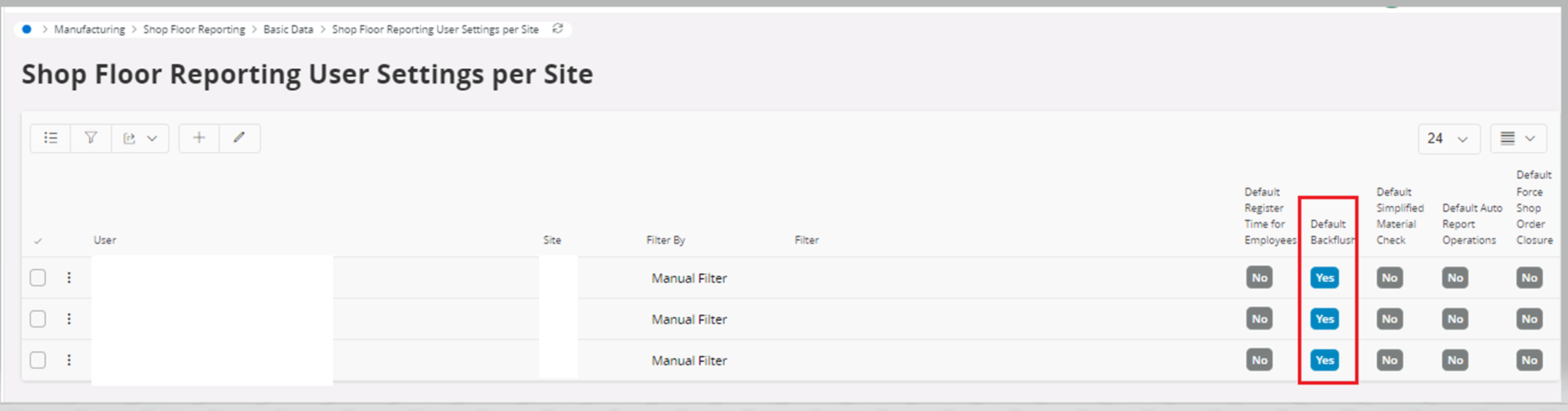
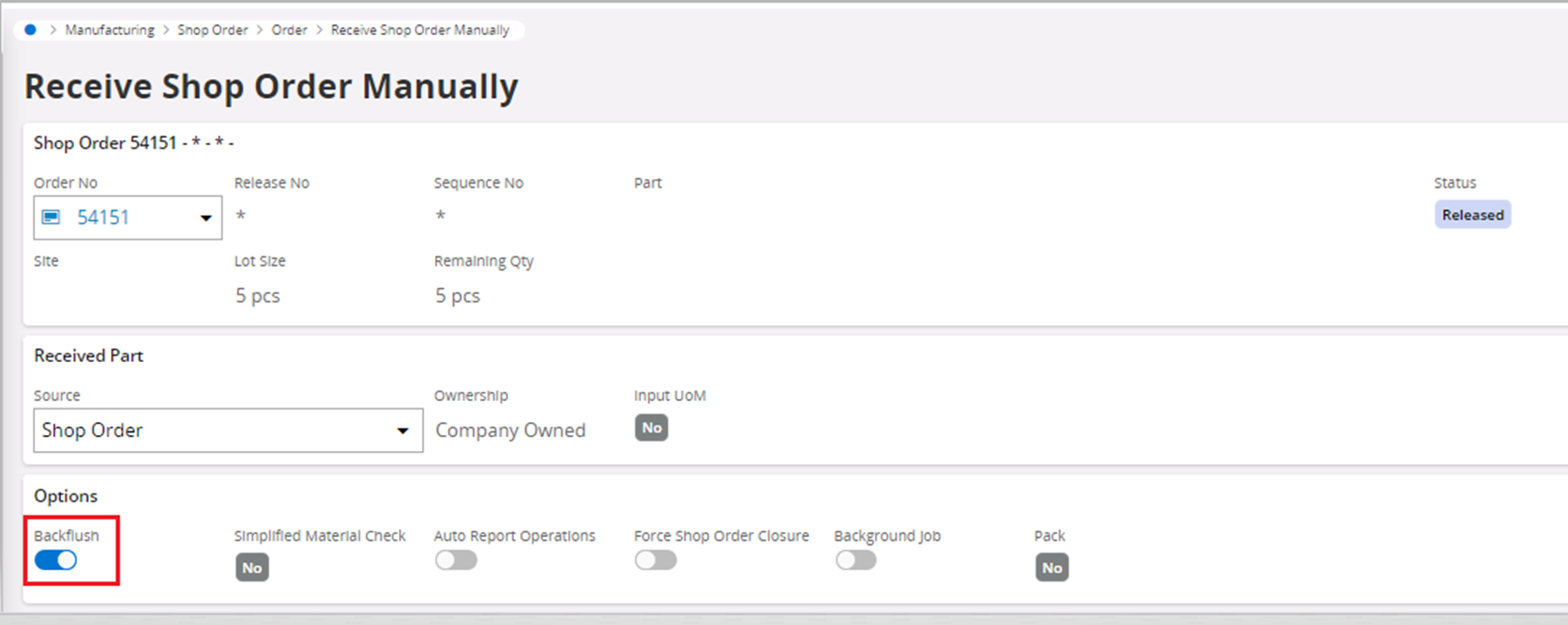
The background for this question is that the customer has developed a way to work for a specific flow (injection molding) in APP9 where it is possible to set the Default backflush setting isolated to SFWB (via RMB properties => Default values for Approve operations). They do not want it to be marked by default in Manual Receive Shop Order but I haven’t found a way to prevent this in standard IFS Cloud if the Default setting is marked. It is not possible to have the Reserved/Issue Method for the components set to manual since the material is in fact backflushed when the operation time is reported when they receive info from their MES regarding how many parts that have been manufactured (every 15 mins). It can take between 4-72 hours before the parts are being received into stock (when the box is full) so the material has to be backflushed when the operation is reported to have a correct inventory balance. The problem is that components to issue can remain on the Shop Order when the part is to be received into stock, and if the operator would forget to unmark the backflush setting, the rest of the material (that has not been used) will be issued when the receipt is done.
This problem could probably be solved by a custom event, but I wanted to place the question since the design of Receive Shop Order has been redone in IFS Cloud and this could be an aspect that more users are affected by. You have to enter the Receive Shop Order Manually via an assistant where it is only possible to query for one order at a time.
Best Regards
Eva