Hi
Hoping for some inspiration here.
I have a parent shop order with a need date of 01/10/2021( approx 1 day build) which contains multiple children of Both manufactured and purchased items.
All manufactured parts set to Finite
After Scheduling Through APB it is giving me planned finished in week 49 . This is despite all manufactured components having been scheduled to be completed by Week 39, Having ample capacity on the necessary work center and all PO’s been received.
I’m also unable to drag it to an earlier date.
This results is making no sense to me, is it possible that i’m missing some other constraint?
Any light shed on the subject is welcome
Ian
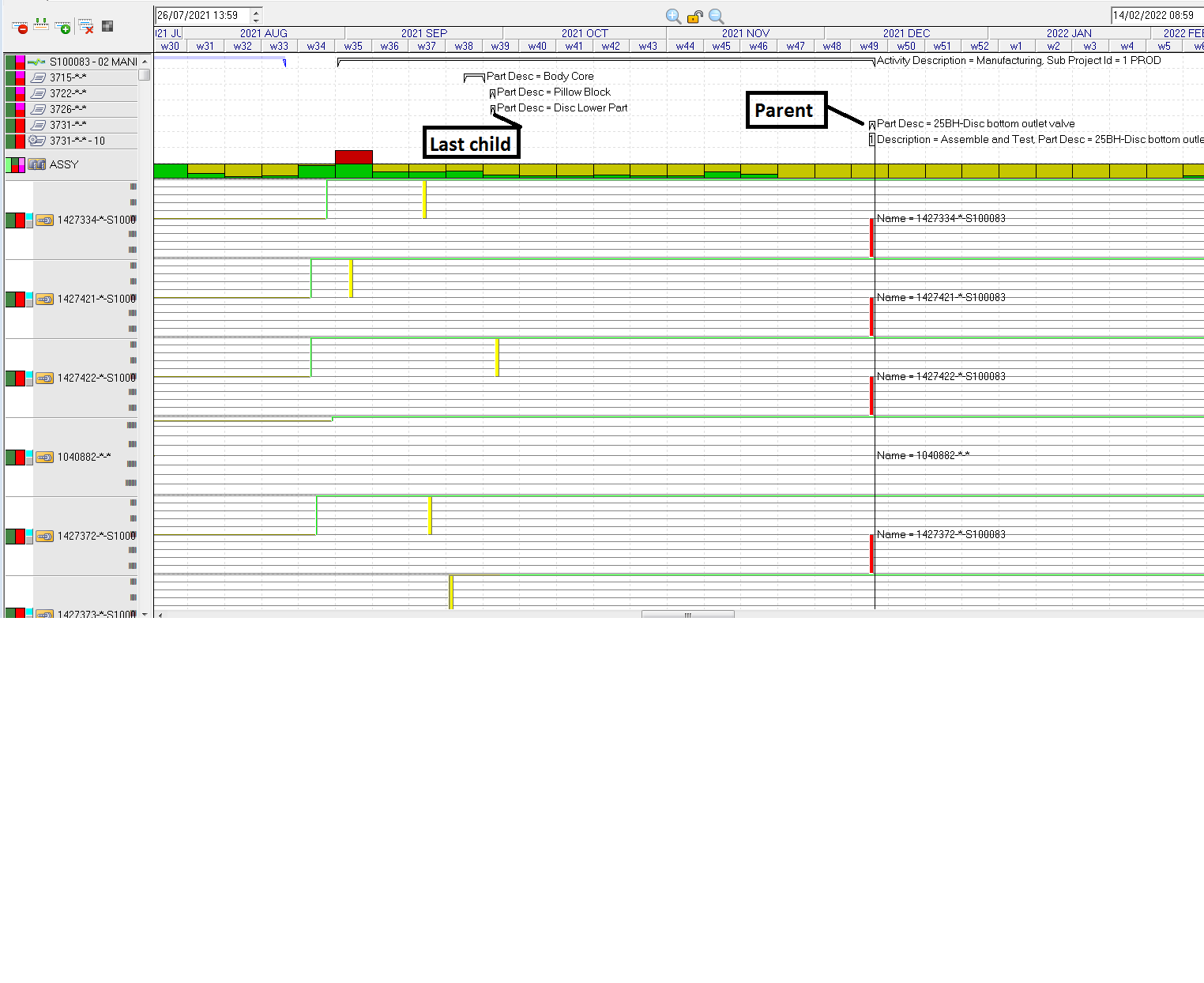