We are looking for a good way to measure equipment down time. Currently we start the down time when the fault report is created. We then mark the up time as when the work order is closed. The issue we have with this is sometimes we can get the equipment running, so it is not down, but it is not completely fixed either. We are waiting for parts to arrive to complete the fix. We can’t close the work order if there are open PO items on it, so how can we capture that the machine is no longer down?
Page 1 / 1
Hey
What is the use case? Is this for reporting purposes only?
How about using dedicated fields to capture equipment down/up times?
Cheers!
see also below
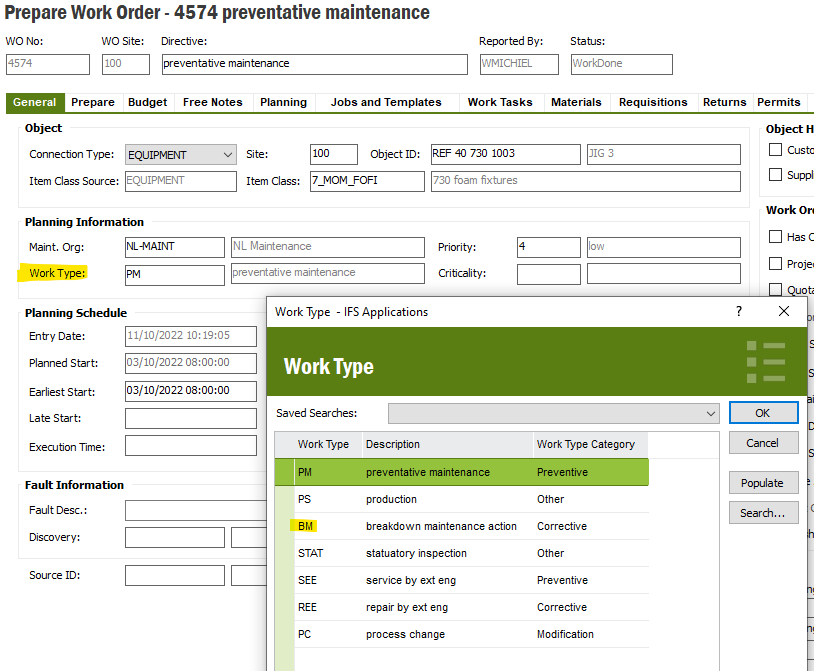
What I further would like to try is to calculate the relative downtime. An action could also be repaired or fail outside the scheduled time. I don't know how, but I think I have to create a calculation with calendar data.
Reply
Enter your E-mail address. We'll send you an e-mail with instructions to reset your password.