We use the shop orders material planning (SOMP) screen to quickly identify shop order shortages. We do not want consider material available until is has completed QA inspection and is approved for use. We currently use the availability control ID field to identify when material is waiting for inspection, approved or rejected. We are running into an issue where materials are received and awaiting QA inspection but the SMOP screen shows the material as available to use. We want the material to show as on hand but not available which then triggers the SMOP to call it out as a shortage. We tried setting the awaiting QA inspection availability control id status to non-nettable but that caused MRP to drive additional purchases for the materials that were just received. Is there an inventory status that can be used that recognizes the material as on hand but not available? Or has anyone else run in to this issue and found another way to easily identify material shortages due to awaiting QA inspection?
Unless all of the material you have for a given location is in inspection, you may run into issues with the availability control as it will apply to all quantity in that location.
We first segregate the material by having it in a separate warehouse from freely useable inventory AND apply the availability control there, never in regular inventory. That is just our practice and secondary to your question.
The problem you are seeing can’t be fixed by the Availability Control unless you use the Non-nettable setting, but as you’ve realized, that causes a bad side effect of creating more supply. Even when segregated in another warehouse, if the material will be viable, even IPAP will continue to see it as available, which is essentially the same as the SOMP screen.
You can have the Availability Control set to prevent reservations or issuing, but I don’t know of a way on IPAP or SOMP to reduce the available on hand displayed only when it is in inspection, but will later become available.
If the inspection is invoked at the point of receipt using the Receive into Arrival, Inspect at Arrival Receive Case (SfPP setting). This will place the item in Inspection Management, while it is in the Arrival location which can only be used as part of the PO Receipt Inspection, then you can block the item from being seen as available.
Here is an example:
Two demands for the part, the first one is reserved, so not available for the second order. But I have a PO in Arrival awaiting inspection. The available on IPAP shows 0.
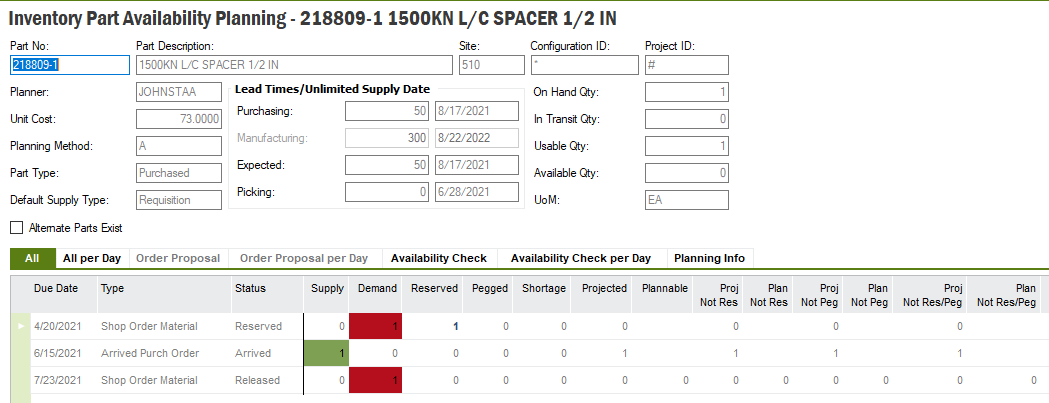
And on SOMP, the item shows that there is a Useable Qty of 1 (the one that is reserved on the other order, but the one that is on the Arrived PO is not yet seen as either Useable or Available.

Enter your E-mail address. We'll send you an e-mail with instructions to reset your password.