Hi All,
I am working with an aircraft OEM and they manage different kind of rotable pools with their customers wherein customer can take a part from the rotable pool and in-return will supply the unserviceable core item to the OEM for repair.
This OEM does not carry out internal repairs and create a CRO of repair order type “external service order” to send the unserviceable core part (P1) to supplier and get it repaired. Some of the times, the supplier will perform modification to the part (P1) which leads to change of part number (P1 now becomes P2). When we receive the modified part (P2), OEM would perform Register Arrival - utilize modify receipt conditions and change the part number (P2 - ensure alternates are defined) and receive the modified part (P2) in inventory. This creates a part serial transaction for the received modified part and serial.
Now the caveat over here is, the CRO external order which was initially created for the unserviceable part P1 remains open and under the transaction tab of CRO, it shows current position of P1 as Issued and that does not allow us to change the status of CRO order to completed/closed.
Refer this screenshot of part serial
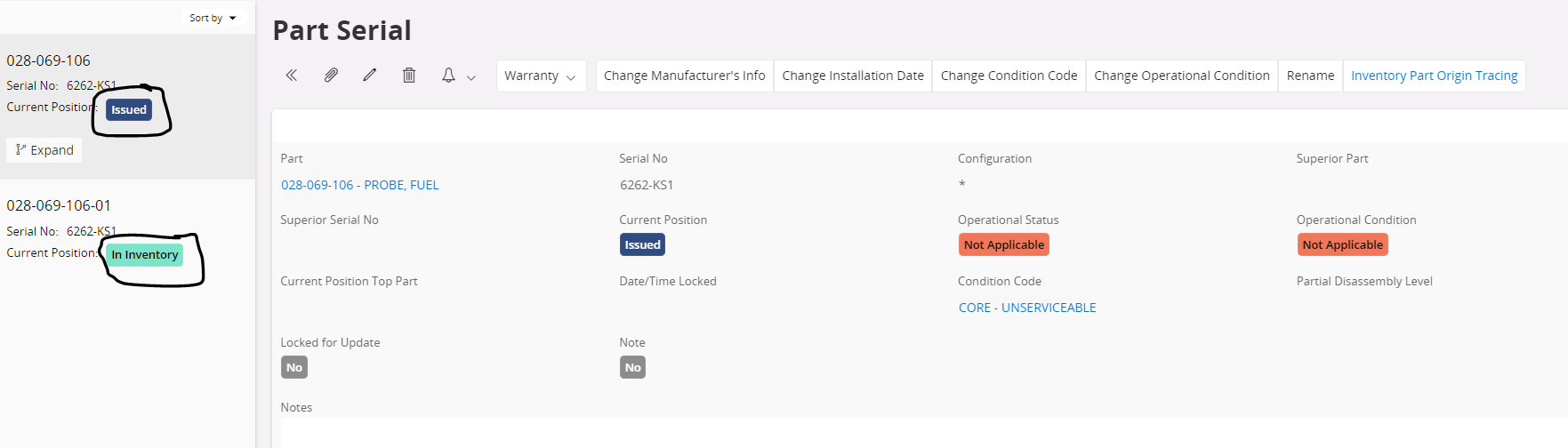
P2 (modified part number) is 028-069-106-01 which is received from supplier shows as In Inventory
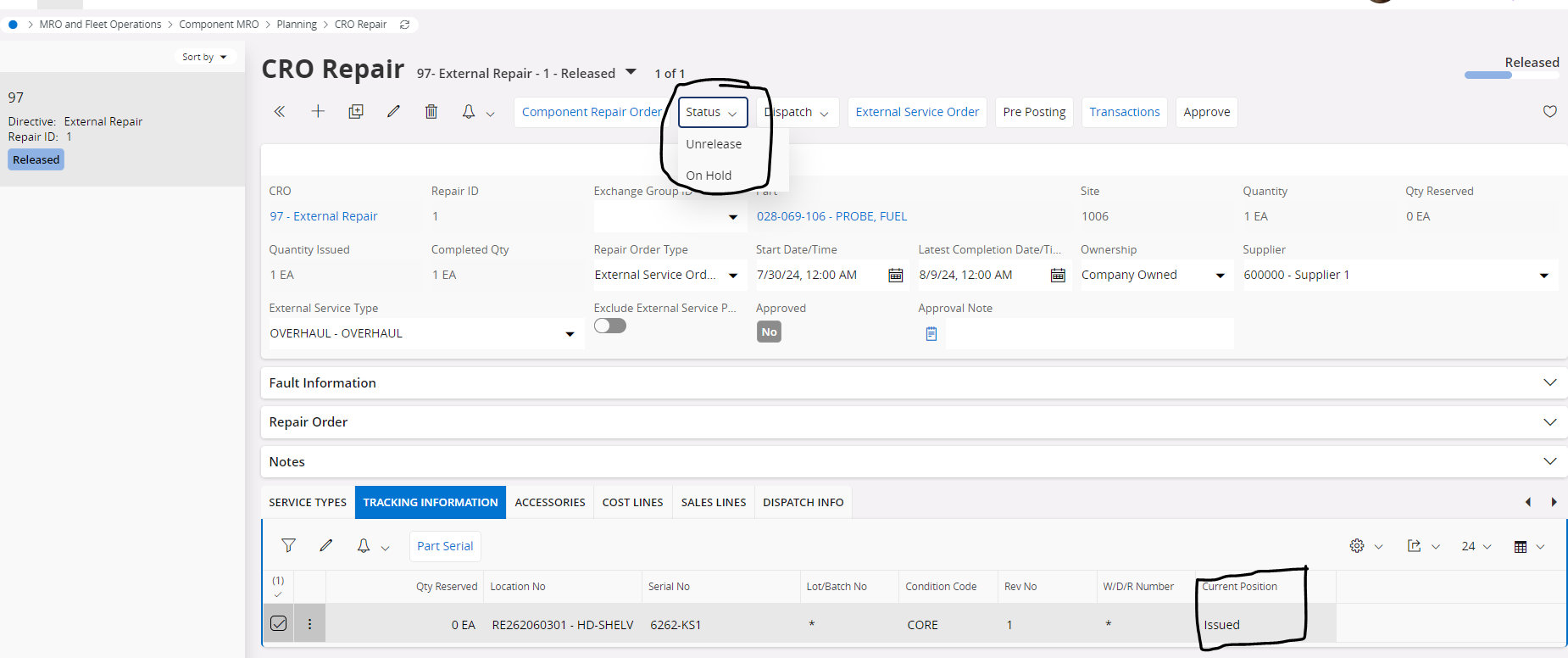
Looking for a solution which is as per the regular MRO industry standards.
Thank you
Kunal